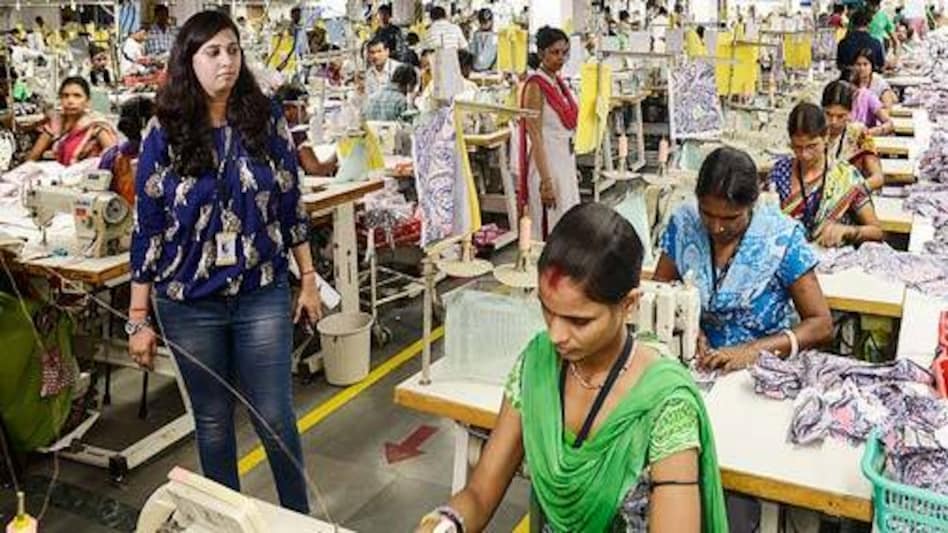
How is the Indian textile sector placed?
India has the ecosystem from fibre to fashion, both in cotton and man-made fibre, an abundant and young labour force, a vibrant domestic market and a good second largest exporter of textiles, apparel and made-ups in the world. Currently, the imports into India for apparel, made-up and textile items are low but there are specific segments where they are growing rapidly. These include Moisture Management Fabric (MMF) and technical textiles. As wage cost is rising and Yuan gaining strength, apparel industry is shifting base from China, creating a potential market of $280 plus billion for other countries. India is uniquely positioned to capitalize on this opportunity.
What are the big issues that the sector is facing?
There are key challenges which need to be addressed. Setting and scaling up: the textile sector was traditionally reserved for Small Scale Industries (SSIs) de-reserved in late 2000 year. The largest Indian apparel and made-ups factory will employ 3000-4000 people, large Chinese factories employ over 10,000 people at one place. Some even go up to 30,000 people. Significant attempts have been made to increase the scale in Indian industry but the key issues revolve around - labour, land and building, enabling infrastructure such as power and connectivity. Unfavourable labour environment: The fear of managing large number of employees has dissuaded several enterprises from growing. Some states have introduced progressive reforms to benefit the industry, still majority are far from adopting progressive reforms. The biggest capital cost components for an apparel factory are the land and building costs which is more than 50 per cent. Issues related to land acquisitions have deterred entrepreneurs from venturing into large scale manufacturing. Our clusters are fragmented and lack clear positioning in the minds of Buyers.
High operating cost: It has two aspects. The cost side pressures such as - tax, power, wage, wage increases and other is labour productivity. The sector is highly labour intensive. The wage cost can go up from 6 to 8 per cent of the overall cost base in yarn to as high as 30-40 per cent in the case of apparel. Synthetic value chain is very poor despite huge raw material base. The lack of local fabric availability at the right quality and at competitive prices leads us to resort to importing MMF fabrics. Such imports result in loss of drawback on exports of apparel made from such imported fabric. Another issue is differential treatment of cotton (0) and synthetic (12.5 per cent) products in terms of excise duty. Energy cost is higher in Gujarat and Maharashtra compared to rest of the country, where fabric and yarn production is concentrated. Labour productivity is poor than countries like Bangladesh, mainly due to poor working conditions, insufficient training and high attrition rates. Market barriers: Higher duty on synthetics and lower drawbacks as compared to competitors is another major factor. This make synthetic segment uncompetitive. The cost disadvantage ranges from 2 to 11 per cent. China has maximum VAT rebate for textile and apparel exporters of 17 per cent, whereas India allows a drawback of around 7-11 per cent. Trade barriers is another issue. Logistic Challenges: both in domestic and export markets logistics is a challenge. Be it land ports (ex. Petrapole) or sea ports (JNPT) customs procedures and clearances take more time than other countries. India suffers 2-3 week disadvantage against China and one week gap against Vietnam on logistics. Investment and financing entrepreneurship is an issue: TUFS is an important scheme by government but its benefits has gone towards the spinning sector. As time to market is important in fashion industry, Indian manufacturers are not able to complete as cost of working capital is high. Indian Manufacturers are not able to stock up fabric for upward processing as compared to China & Vietnam. India takes on an average 63 days from placement of PO till shipment from Mill. While china takes 31 days and Vietnam takes 46 days. Lack of investment in knit technology and other latest processing technology.
Where do you think India needs to catch up to be a global market leader?
Firstly, build scale to suit the fabric of Indian society, as the industry is highly labour intensive, introduce flexible labour laws; job linked support schemes, innovative hub and spoke models for apparel/textile parks to employ labour in hinterlands and introduce PPP models for Industry to provide scale and create jobs. In India, share of companies with revenue more than 200 million is 3 per cent while in China it is 14 per cent and in Bangladesh it is 7 per cent. Secondly, bridge the operating cost gap, especially on synthetics. Entrepreneurs need to aggressively drive up productivity by investing in world class facilities, process improvements and build a culture of manufacturing excellence. Simplified tax structures and neutral implementation of GST for both cotton and synthetic products will give the much required boost to the industry. Thirdly, infrastructure, especially at ports, import facilities and clearance procedures should be streamlined to cut turnaround times.
Signing FTAs with major markets like the European Union can equalise market access positions with key competitors like Bangladesh. Bangladesh has zero duty access to EU, Vietnam is on its way, India has 10 per cent duty, while China has 12 per cent duty on cotton shirt. Fourthly, increased investments in technology, especially processing and technical textiles either through capital subsidy or technology partnerships. The A-TUFS released in December 2015 has taken welcome steps in this respect. Fifthly, Indian entrepreneurs need to invest both financial and human resources on technology and innovation to address the constantly evolving markets. Investments are required in technical textiles, processing, and apparel making in particular. India needs to create its own 'silicon-valleys' for technical textiles, with a full ecosystem of investors, start-ups, production facilities and ultra-fast clearances. Ease of doing business is equally critical for innovation.
Which segment within the textile supply chain is the weakest? And what can be done to boost it?
Fabric and processing are the weakest segments of the value chain. However, need is to provide end to end solution for the entire value chain. Global brands like PVH, H&M, GAP etc see India's end to end ecosystem as one of our value propositions in replacing China. In order to strengthen the value chain, synthetics industry needs support in the form of GST neutral rates for cotton/MMF; synthetic fiber should be available at international rates, power cost rationalization; global competitiveness, drawback scheme similar to China under GST; adjust export drawback in the interim to reflect state taxes (depends on final drawback rates notified by Government); capital cost rationalization.
Though India is a leader in the yarn space, where and how does it lose the edge in the processing and fabric stage?
The processing and fabric segments are highly fragmented and comprising of SSIs. China is a leading in fabric exports globally, accounting for over 45 per cent of all global fabric exports in 2014. India is relatively poor in knits category due to lack of technology and investment, while global market is moving towards knit category. The imports of knit fabric is rising rapidly, which needs to be curtailed through better sufficiency in these segments which can be achieved by strong processing facilities in India. In apparels, India's domestic and global position in apparel has been relatively strong compared more developed economies but has underperformed peers like Bangladesh, and Vietnam who have seen growth rates of over 18% per annum over the last five years compared to India which has averaged 9 per cent in most categories. India's competing countries are having duty free access in major markets, USA and EU. This make Indian textile products highly uncompetitive in these markets.
The cabinet has approved the new textile package… how do you think it will benefit the textile supply chain?
The special package announced recently is expected to boost competency of textile and apparel exports in international markets. The seasonal flexibility i.e. increases in overtime limit from 50 hours to 100 hours and introduction to fixed term employment are already addressed by Government in the special package. This will help the sector to attain scale of production.
With EPF scheme reforms and overtime caps, introduction of fixed term employment, additional incentives under TUFs, industry will be encouraged to increase scale and capacity.
Enhanced duty drawback will encourage competitiveness of Indian exports in foreign markets. It is equally important to protect the entire value chain. Spinning, weaving, processing sector are the key segments of the value chain which is supplying raw material to the apparel sector. Supporting these segments will benefit the entire textile and apparel industry to attain competitiveness.