Going, Going, Gone: Automation can lead to unprecedented job cuts in India
As automation spreads, millions of jobs could be on the block. What's the way out?
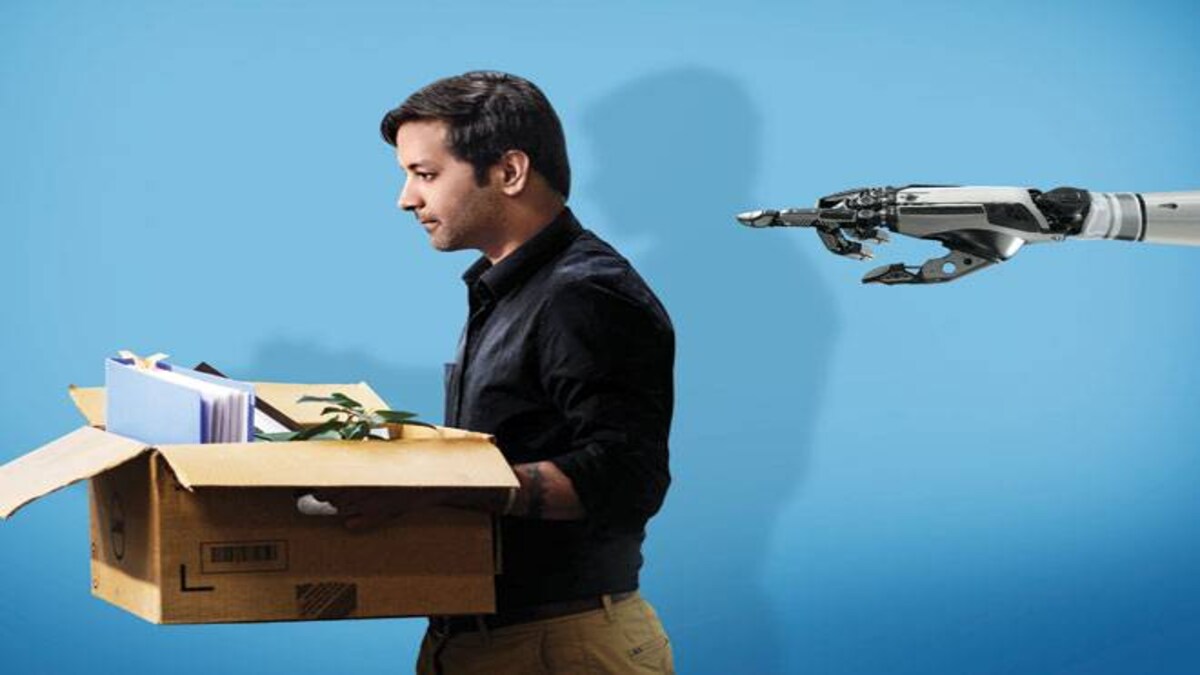
- Jun 1, 2017,
- Updated Dec 26, 2017 9:58 PM IST
It's like a large server. Except that the grey and orange box has a camera on top and another at the bottom. It screeches, almost as if to say 'I'm working'. One camera reads the route as it suddenly moves sideways and then springs forward a few metres before parking below a rack that can hold up to 500 kg of raw materials, finished goods and parcels. Another screech and it's ready to advance along the rack. In large warehouses, it can move racks at two metres a second.
The box is a robot, part of a storage and order picking system for warehouses that Gurgaon-based start-up GreyOrange has developed. A large e-commerce warehouse can employ up to 200 such robots, called Butlers. They can swarm around like bees for 24 hours without tiring; when low on battery, they automatically dock at a charging station. It takes 30 minutes to charge, or roughly the time humans take for a lunch break.
A warehouse no longer needs men to push trolleys. The server that controls the robot analyses, re-slots the racks and audits inventory "dynamically". One Butler can replace more than one human - a corporate video from the company says the system can result in a 60-80 per cent reduction in manpower. GreyOrange's robots have already been deployed in the warehouses of Flipkart, DTDC, Mahindra, Delhivery, and Aramex, among others. The start-up has moved on - besides e-commerce warehouses, it is now automating manufacturing companies as well. Often, where a Butler's job ends, other robots take over. They can pick the raw material from racks and feed it to machines, doing away with the need for many semi-skilled shop floor workers.
At Honda's new scooter plant at Vithalapur, 80 kms from Ahmedabad, the thunder from its press machines is near deafening. Five giant robots, bought from ABB, orchestrate operations instead of men. Two of them lunge forward, sense metal sheets, pick them up before placing them onto the press that shapes scooter fuel tank frames. The third and fourth robots collect the shaped metal, twist, and feed a second press where the shape is trimmed. And the fifth picks the finished frame and pushes it onto a table. The press shop today produces 4,500 fuel tank frames in 16 hours and 8,200 components overall.
Only 14 people work here in two shifts. Without robots, a manual press shop of this magnitude would have required 72 men. The Vithalapur factory, Honda's fourth two-wheeler plant in India, is one of the most automated in the world. The company's first plant in Manesar has 65 automation processes; the fourth has 241. While Manesar requires one person to produce one vehicle, Vithalapur does it with 0.64 - that's a 36 per cent jump in productivity. A similar script is being written in many green-field manufacturing plants across the country. Everywhere, it is about doing more with less - less people.
That's because price realisation is a challenge. There are only two levers to retain margins on a product: cost reduction or increase in the product price. Price increase is limited, thanks to competition. Manufacturers across the world, and in India, are therefore resorting to an unparalleled use of technology to flatten costs. The fallout, in almost every case, is "technological unemployment", a term popularised by economist John Maynard Keynes in the 1930s.
This term, strangely, is still valid. However, unlike the 1930s, the technological unemployment of this decade is likely to be of a far serious order, and one that cuts across every conceivable sector - from e-commerce and manufacturing to banking, agriculture as well as IT services and BPO.Think of software engineers. Knowing how to code has been the surest way of securing a good life for Indians over the past two decades. In fact, some states such as Andhra Pradesh have an oversupply of engineering colleges. But the advent of Artificial Intelligence, or AI, has meant that machines can now be trained to carry out many standardised tasks software engineers do. Likewise, think of drones that can spray pesticides across farms or identify sick plants that need attention, doing away with the need for labour. Or take condominiums where hi-tech entry systems reduce the need for security guards. Or driverless cars of the future that can hit the livelihoods of professional drivers. Or machines to make pizzas or burgers, because the process is repetitive, just like manufacturing a car.
Momentum Machines, a San Francisco-based 'collective of foodies and engineers' claims to have built a robot that can make gourmet burgers without human intervention. In an era where economies are so 'coupled', it takes little time for technologies to cross borders. The job crisis is for real and it raises several uncomfortable questions. How many jobs will the present era of technology unemployment vaporise in India? Will it impact just the bottom-of-the-pyramid employees or also middle-level workers? Can technology replace the highly-skilled? If the composition of employment changes in one industry, will those employees find jobs elsewhere? And what must India do to mitigate the risks associated with high unemployment? Turns out, there are no easy answers.
It's like a large server. Except that the grey and orange box has a camera on top and another at the bottom. It screeches, almost as if to say 'I'm working'. One camera reads the route as it suddenly moves sideways and then springs forward a few metres before parking below a rack that can hold up to 500 kg of raw materials, finished goods and parcels. Another screech and it's ready to advance along the rack. In large warehouses, it can move racks at two metres a second.
The box is a robot, part of a storage and order picking system for warehouses that Gurgaon-based start-up GreyOrange has developed. A large e-commerce warehouse can employ up to 200 such robots, called Butlers. They can swarm around like bees for 24 hours without tiring; when low on battery, they automatically dock at a charging station. It takes 30 minutes to charge, or roughly the time humans take for a lunch break.
A warehouse no longer needs men to push trolleys. The server that controls the robot analyses, re-slots the racks and audits inventory "dynamically". One Butler can replace more than one human - a corporate video from the company says the system can result in a 60-80 per cent reduction in manpower. GreyOrange's robots have already been deployed in the warehouses of Flipkart, DTDC, Mahindra, Delhivery, and Aramex, among others. The start-up has moved on - besides e-commerce warehouses, it is now automating manufacturing companies as well. Often, where a Butler's job ends, other robots take over. They can pick the raw material from racks and feed it to machines, doing away with the need for many semi-skilled shop floor workers.
At Honda's new scooter plant at Vithalapur, 80 kms from Ahmedabad, the thunder from its press machines is near deafening. Five giant robots, bought from ABB, orchestrate operations instead of men. Two of them lunge forward, sense metal sheets, pick them up before placing them onto the press that shapes scooter fuel tank frames. The third and fourth robots collect the shaped metal, twist, and feed a second press where the shape is trimmed. And the fifth picks the finished frame and pushes it onto a table. The press shop today produces 4,500 fuel tank frames in 16 hours and 8,200 components overall.
Only 14 people work here in two shifts. Without robots, a manual press shop of this magnitude would have required 72 men. The Vithalapur factory, Honda's fourth two-wheeler plant in India, is one of the most automated in the world. The company's first plant in Manesar has 65 automation processes; the fourth has 241. While Manesar requires one person to produce one vehicle, Vithalapur does it with 0.64 - that's a 36 per cent jump in productivity. A similar script is being written in many green-field manufacturing plants across the country. Everywhere, it is about doing more with less - less people.
That's because price realisation is a challenge. There are only two levers to retain margins on a product: cost reduction or increase in the product price. Price increase is limited, thanks to competition. Manufacturers across the world, and in India, are therefore resorting to an unparalleled use of technology to flatten costs. The fallout, in almost every case, is "technological unemployment", a term popularised by economist John Maynard Keynes in the 1930s.
This term, strangely, is still valid. However, unlike the 1930s, the technological unemployment of this decade is likely to be of a far serious order, and one that cuts across every conceivable sector - from e-commerce and manufacturing to banking, agriculture as well as IT services and BPO.Think of software engineers. Knowing how to code has been the surest way of securing a good life for Indians over the past two decades. In fact, some states such as Andhra Pradesh have an oversupply of engineering colleges. But the advent of Artificial Intelligence, or AI, has meant that machines can now be trained to carry out many standardised tasks software engineers do. Likewise, think of drones that can spray pesticides across farms or identify sick plants that need attention, doing away with the need for labour. Or take condominiums where hi-tech entry systems reduce the need for security guards. Or driverless cars of the future that can hit the livelihoods of professional drivers. Or machines to make pizzas or burgers, because the process is repetitive, just like manufacturing a car.
Momentum Machines, a San Francisco-based 'collective of foodies and engineers' claims to have built a robot that can make gourmet burgers without human intervention. In an era where economies are so 'coupled', it takes little time for technologies to cross borders. The job crisis is for real and it raises several uncomfortable questions. How many jobs will the present era of technology unemployment vaporise in India? Will it impact just the bottom-of-the-pyramid employees or also middle-level workers? Can technology replace the highly-skilled? If the composition of employment changes in one industry, will those employees find jobs elsewhere? And what must India do to mitigate the risks associated with high unemployment? Turns out, there are no easy answers.