The India Potential
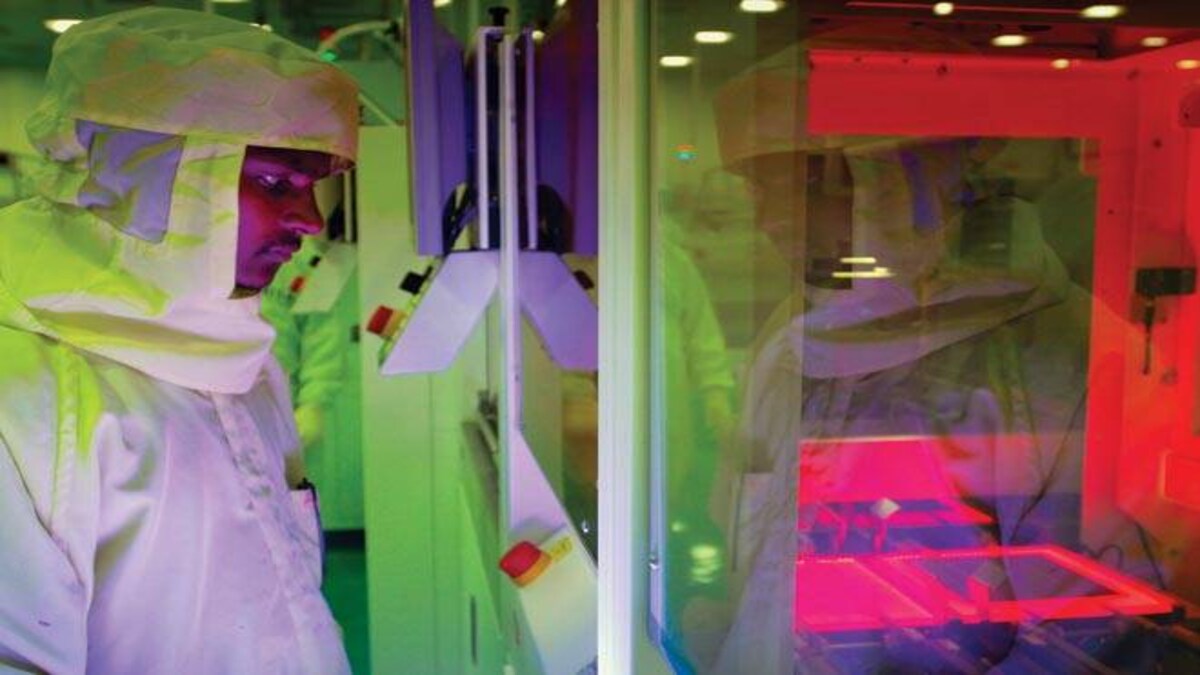
- Dec 26, 2016,
- Updated Jan 3, 2017 4:23 PM IST
VUCA - a term introduced at the end of the Cold War to reflect volatility, uncertainty, complexity and ambiguity - has gripped organisations with change in our markets. It is often driven by disruptive technologies, new mobility solutions, connectivity, new players entering the market, and new legislations. The repercussions are tremendous, but survival is the core nature of successful collaborations between the demands of the market and the ability of an organisation to cater to these needs. India is the best example of a market that consistently keeps bouncing back into the green. The Make in India initiative, for instance, has opened new horizons for the manufacturing industry, and highlighted the importance of the quality of goods manufactured, the localisation of various processes, a strong bond between the Indian government and manufacturers, and, largely, a positive impact on the economy.
India's manufacturing sector has the potential to touch $1 trillion by 2025. It is likely that the sector will account for 25-30 per cent of the country's GDP, and create up to 90 million domestic jobs by 2025. Emerging from the shadow of the services sector, the manufacturing industry can seize more of the global market, now more than ever. With business conditions in the Indian manufacturing sector booming, a market of more than a billion consumers and increasing purchasing power, a few questions come to mind: what does all this mean for manufacturing in India? What changes must one expect? Are there opportunities or risks? What is the approach one must take to be successful? Are we prepared for the future?
The future of manufacturing belongs to those who think 10 steps ahead, who leap in bounds and still emerge at the top. Catering to the future involves an emulsion of innovative and holistic new technology that increases efficiency, automation of technology to eliminate errors and drive consistency, and the digital connectivity to do so. To get the most out of Industry 4.0 technologies, and to get past square one with a digital business model, companies must prepare for digital transformation. Data management and cyber security will be the most critical problems to solve. India however, is equipped with the technological know-how and the best resources that money can buy. But the most significant of all is the Digital India initiative by the government of India. This ties in other processes that sync together harmoniously, and opens the market for new players in the industry with renewed income resources that impact the economy.
Changes in the manufacturing industry, however, do not act on technology alone. Leaders play a pivotal role in steering the path that technology takes. Having a greater vision for the future that is not limited to what we know of the past, but one that is dynamic enough to absorb advanced ideas and a sense of the impossible can revolutionise the industry. Not only do leaders make key decisions, they are the guiding forces that influence an organisation.
Another aspect of changing dynamics in manufacturing is to have an increasingly positive impact on the planet. The move towards the future is more aligned with a clean and green environment. The term "green" manufacturing can be looked at in two ways: the manufacturing of 'green' products, particularly those used in renewable energy systems and clean technology equipment of all kinds, and the 'greening' of manufacturing - reducing pollution and waste by minimising natural resource use, recycling and reusing what was considered waste, and reducing emissions. A green earth is the new cool, but unlike a fad, it has real consequences.
Manufacturers of the future are making sure that production processes are environmentally friendly. CO2 emissions have been downsized with the use of renewable resources like solar and wind power. India's growth in the renewable energy sector will only aid manufacturers in creating sustainable and smart factories.
VUCA - a term introduced at the end of the Cold War to reflect volatility, uncertainty, complexity and ambiguity - has gripped organisations with change in our markets. It is often driven by disruptive technologies, new mobility solutions, connectivity, new players entering the market, and new legislations. The repercussions are tremendous, but survival is the core nature of successful collaborations between the demands of the market and the ability of an organisation to cater to these needs. India is the best example of a market that consistently keeps bouncing back into the green. The Make in India initiative, for instance, has opened new horizons for the manufacturing industry, and highlighted the importance of the quality of goods manufactured, the localisation of various processes, a strong bond between the Indian government and manufacturers, and, largely, a positive impact on the economy.
India's manufacturing sector has the potential to touch $1 trillion by 2025. It is likely that the sector will account for 25-30 per cent of the country's GDP, and create up to 90 million domestic jobs by 2025. Emerging from the shadow of the services sector, the manufacturing industry can seize more of the global market, now more than ever. With business conditions in the Indian manufacturing sector booming, a market of more than a billion consumers and increasing purchasing power, a few questions come to mind: what does all this mean for manufacturing in India? What changes must one expect? Are there opportunities or risks? What is the approach one must take to be successful? Are we prepared for the future?
The future of manufacturing belongs to those who think 10 steps ahead, who leap in bounds and still emerge at the top. Catering to the future involves an emulsion of innovative and holistic new technology that increases efficiency, automation of technology to eliminate errors and drive consistency, and the digital connectivity to do so. To get the most out of Industry 4.0 technologies, and to get past square one with a digital business model, companies must prepare for digital transformation. Data management and cyber security will be the most critical problems to solve. India however, is equipped with the technological know-how and the best resources that money can buy. But the most significant of all is the Digital India initiative by the government of India. This ties in other processes that sync together harmoniously, and opens the market for new players in the industry with renewed income resources that impact the economy.
Changes in the manufacturing industry, however, do not act on technology alone. Leaders play a pivotal role in steering the path that technology takes. Having a greater vision for the future that is not limited to what we know of the past, but one that is dynamic enough to absorb advanced ideas and a sense of the impossible can revolutionise the industry. Not only do leaders make key decisions, they are the guiding forces that influence an organisation.
Another aspect of changing dynamics in manufacturing is to have an increasingly positive impact on the planet. The move towards the future is more aligned with a clean and green environment. The term "green" manufacturing can be looked at in two ways: the manufacturing of 'green' products, particularly those used in renewable energy systems and clean technology equipment of all kinds, and the 'greening' of manufacturing - reducing pollution and waste by minimising natural resource use, recycling and reusing what was considered waste, and reducing emissions. A green earth is the new cool, but unlike a fad, it has real consequences.
Manufacturers of the future are making sure that production processes are environmentally friendly. CO2 emissions have been downsized with the use of renewable resources like solar and wind power. India's growth in the renewable energy sector will only aid manufacturers in creating sustainable and smart factories.