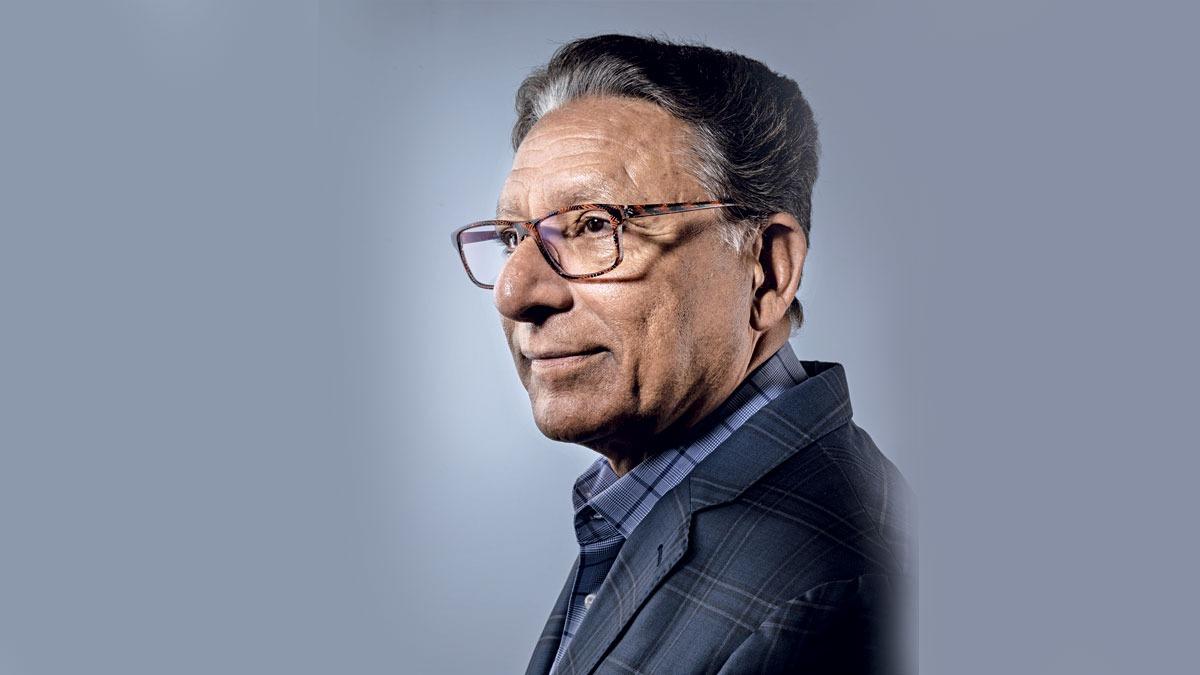
The semiconductor shortage in recent years has brought forth how critical a resource it is for the global economy. This shortage, which was aggravated by disruptions to the global supply chain, led countries in the space to double down on manufacturing, while some which did not have manufacturing facilities decided to set them up. Although late, India extended its vision for AatmaNirbharBharat to semiconductor chips with the India Semiconductor Mission (ISM)—which has a financial outlay of Rs 76,000 crore—on December 15, 2021. For years, India has dreamt of mass-manufacturing chips, and to help it on the journey, it has set up an advisory committee for ISM. One of the members of the committee is Vinod Dham, popularly known as the ‘father of the Pentium chip’. The 72-year-old, in a freewheeling interview with Business Today’s Nidhi Singal, says that setting up semiconductor manufacturing is a Herculean task, and details India’s collective effort to make it possible. Edited excerpts:
Q: It has been a year since the government announced the semiconductor scheme. What has the progress been so far?
A: ISM is being led by global experts in the semiconductor and display industries. It acts as the nodal agency for efficient and smooth implementation of the schemes to set up semiconductor and display fabs. We have already received several proposals in the areas of chip fab, display fab, packaging and design. These are in various stages of due diligence to establish the fit and eligibility qualifications for approval. Several advisory working groups have been set up to accelerate the pace of due diligence. Each group has key domain experts who weigh [in with] their expertise on the proposals. Considering how recently this scheme was launched, I believe very good progress has been made to date.
I cannot tell you about the approvals on the proposals received… but considering this is ‘Mission Impossible’, we have collectively undertaken to make it ‘Mission Possible’. I am pleased with the progress that we’ve made so far.
Q: Does every government take this long to take a call on fabs?
A: Let me give you a very current reference. The US, the leader in the semiconductor world, passed the ‘CHIPS for America Act’ [the Creating Helpful Incentives to Produce Semiconductors and Science Act of 2022] to invest $280 billion to bolster US semiconductor capacity, catalyse R&D and create regional high-tech hubs and a bigger, more inclusive STEM workforce. The Act was first proposed in June 2020 and approved in August 2022. Even for this leading semiconductor nation, it will take a decade or more to implement the scheme and the plans.
Similarly, India’s Union Cabinet approved the ‘Semicon India Program’ on December 15, 2021, for the development of semiconductors and the display manufacturing ecosystem in India. However, since we in India are—for all practical purposes—starting from scratch to building an entirely new industry, we are facing a much more complex task. Today, we don’t even have enough sufficiently skilled people with knowledge of semiconductors in India. Considering the magnitude and breadth of the task facing us, I think we are beginning to make good progress on many fronts. But this undertaking is not for the faint of heart. And it will take a very long time—decades—to catch up and reach a sustainable threshold. But like I said before, we have to make a start now if we don’t want to be left out.
From here on, typically, once the plans are completed, it should take two to three years to build the fab.
Q: The government has revised the scheme by increasing incentives for compound semiconductors, sensor fabs, and more. What’s your understanding of this move?
A: As we dug into getting a better understanding of India’s product needs and the global semiconductor markets India could serve in the future, it became clear that even the higher nodes and other process tech will be initially critical for the success of the India Semiconductor Mission. Once this was brought to the attention of our savvy ministers, they moved with speed and got the rules changed to ensure that all of them get a flat 50 per cent incentive [for semiconductor fabs].
In matters related to technology, it is especially crucial to have leaders who understand and appreciate the nuances of dealing with technology-related issues, to get the best outcomes in a timely way. PM (Narendra) Modi has deputed two very capable ministers—Ashwini Vaishnaw, Minister of Electronics and Information Technology (MeitY), and Rajeev Chandrasekhar, Minister of State for MeitY. This is the first time, as I recall, that the two ministers assigned for this crucial task have a background in technology. Furthermore, both have degrees in business.
These two government leaders quickly grasp the issues relating to the challenges we are facing and move with start-up like speed to resolve them within various ministries. I’ve been personally dealing with a variety of officials in the Indian government over the past four decades, but now I see a distinct positive change... a real passion and zeal to solve issues and move with speed and a ‘can do’ attitude. I hope this continues to be the case, independent of the ups and downs.
Q: In India, we don’t have a fab ecosystem. We will have to build everything from scratch. What are the challenges we need to resolve?
A: This is a very loaded question and encompasses some of the issues that I have discussed in my meetings with the ministers. There are many challenges that India needs to resolve to build and develop a fab ecosystem.
First, a ‘fab’—a term used to describe a semiconductor manufacturing facility—needs to be in a place with lots of space. For reasons of economics, it is more cost-efficient to build a cluster of fabs close to each other. This location should have a very good supply of water since fabs are big water-guzzlers. Also, the electric supply must be available 24x7, uninterrupted, 365 days a year—except for scheduled maintenance. The power should be free of any glitches, since some of the semiconductor equipment used for building today’s chips require glitch-free power. The location should be in a place protected from natural disasters, especially earthquakes that can, unfortunately, irreparably damage billions of dollars of fab and equipment. In India, where the infrastructure is still not fully developed, and customs clearance can sometimes take weeks, it is imperative that the airport and customs for key components needed for export outside of India be placed right next to the cluster of fabs and the assembly, testing and packaging facilities.
Moreover, the zones where semiconductor fabs and back-end [assembly, testing and packaging] are located should be by law protected from strikes and unnecessary time-off provisions to enable competitiveness in the global markets.
Also, since a state-of-the-art fab can take up to five years before going into full production, not only full financing has to be in place to complete the job on time, but the labour should also be deployed through 365 days round the clock to make sure the fab is ready as quickly as possible. Fabs are very capital-intensive by nature and generating profits fast is an essential consideration in their implementation.
Beyond locating and building structures, we will need a variety of high-purity gases and wafers to fabricate the chips. Initially, we will have to import many of these raw materials from sources outside of our country, but with time, we can bring some of these supplies in-house.
An even bigger challenge than building a fab is ‘filling a fab’—we need a very high volume of chips to fully utilise the fab capacity. If a fab is not run at over 90 per cent-plus capacity round the clock, the chip costs will go up because of poor capacity utilisation, rendering our products uncompetitive.
Q: In your opinion, what technology or nodes should India look at to begin its fab journey?
A: The technology node (also called process node) refers to a specific set of process design rules that enable the technology to shrink to the next viable generation. The smaller the node, the smaller the feature size, producing smaller transistors that are both faster and more power efficient. But the cost of building chips is higher as the cost of equipment for defining the smaller dimensions skyrockets. Over the past 50 years, the process technology has evolved over a score times. Thanks to Moore’s Law, an observation made in the 1960s by my guru Gordon Moore—the co-founder of Intel—we have been able to shrink the size of chips by half every two to three years.
The choice of picking the right technology node is both a function of the products we choose to initially fill our domestic fab with, and where the performance, power and cost needs of these functions will be in the coming years and decades. Also, keep in mind that our domestic fab capacities will not only be filled with products we need for our domestic needs but hopefully also supply some of the export needs of the rapidly growing global semiconductor market that is projected to double from around $500 billion now [that it took 50 years to reach] to $1 trillion in the next decade.
Today the fabrication of chips has progressed from nodes between 180 nanometres (nm) with the older technology to 3-5 nm with the most advanced technologies used to build high-performance computers for cloud computing. For the bulk of India’s needs in the future, 28 nm appears to be the sweet spot, but for now, anything starting with 65 nm and below will be a good start. For example, the strongest-growing segment in the coming decade is likely to be automotive, where demand is projected to triple over the next decade. It is estimated that the bulk of the automotive needs can be met with technologies at 65 nm and below.
However, there is a lot of heavy lifting and perhaps a new round of incentives [is] needed to encourage domestic product design companies to start building local cellphones, laptops, desktops, servers, routers and other products for automotive, communications and industrial segments to substitute imports.
We need to encourage local businesses to build domestic companies like Xiaomi, Oppo, Nokia, Huawei, Lenovo, and Dell. These OEMs should be supported by a supply of locally designed chips. Thus, we also need to create fabless design companies in India like MediaTek, Broadcom, Qualcomm and Marvell. And to make it even more challenging, these two sets of activities—designing and building devices, and designing local chips that go into these devices—need to start now, hand in hand, so that we have ample availability of locally designed chips, available in a timely manner to fill our fabs as they get ready for production.
Q: What are the things that India should be mindful of to not repeat the mistakes made in the past?
A: Frankly, I am not aware of any mistakes that were made by India in the recent past relating to manufacturing chips in India. To the best of my knowledge, never before has the Government of India ever developed such a scheme for encouraging the setting up of a semiconductor fab in India. However, I will be remiss if I failed to share a little-known secret that was shared with me by the late Gurpreet Singh, the founder of Continental Device India Pvt. Ltd (CDIL), a pioneer [in the field of] manufacturing silicon chips and devices [who had been making semiconductors] in Delhi and Faridabad since 1964. CDIL is my first love; this is where I began my career and was the place where I fell in love with semiconductor technology. Not long ago, Gurpreet Singh shared with me that Robert Noyce, the co-founder of Intel, had visited India in 1969 to explore the opportunity of setting up a semiconductor manufacturing facility here. Unfortunately, the government told him that he could only set up a fab that would not exceed hundreds of thousands of chips, [which is] a complete non-starter. I have often wondered how the tides with Taiwan and China may have turned had we allowed Intel to set up a fab in India back then!
However, there are many things India should keep in mind as it embarks on this vital journey. The semiconductor process tech is not static; the nodes are moving targets. Hence a large amount of capital investment is needed every time the process needs to be moved to the next generation. Private businesses, especially in India, shy away from heavy capital-intensive projects in favour of quick return-on-investment businesses, which are aplenty in the field of software, especially software services. Therefore, the Indian government will have to play a large role in continuing to support the investments for the proliferation of the semiconductor ecosystem and related industries.
Also, if you analyse the $280 billion the US has recently approved under their CHIPS Act, the bulk of it has been allocated for R&D. This is where the new processes, materials and technologies get innovated for continuing the rapid progress we have made in technology over the past 50 years. ISM has been exploring opportunities to set up an R&D centre to develop intellectual property and catch up with the rest of the world on new chips and packaging technologies.
Last but not least, there is a paucity of semiconductor know-how in India. Even though we have tens of thousands of design engineers currently working with the who’s who of the world’s top multinational semiconductor companies in India, there are hardly any semiconductor engineers trained in the knowledge of device physics and process technology that is essential for fabricating and manufacturing chips designed by the design engineers. Once again, ISM has already put the spotlight on this issue, and many parallel efforts are in place to start addressing this.
The semiconductor industry started 50 years ago and has been rapidly evolving since then. We are entering it many decades late, so the job of creating an entire new universe of semiconductors is daunting, to say the least. We have no choice but to undertake this enormous challenge for the critical importance it holds for India’s future economic prosperity and defence.
This complex and multifaceted task of creating an entire semiconductor ecosystem will require a very long time to get established. To achieve success, we will need to have patience, remain steadfast and consistent, and pursue it relentlessly despite the many ups and downs that will be encountered along the way.
@nidhisingal