Going, Going, Gone: Automation can lead to unprecedented job cuts in India
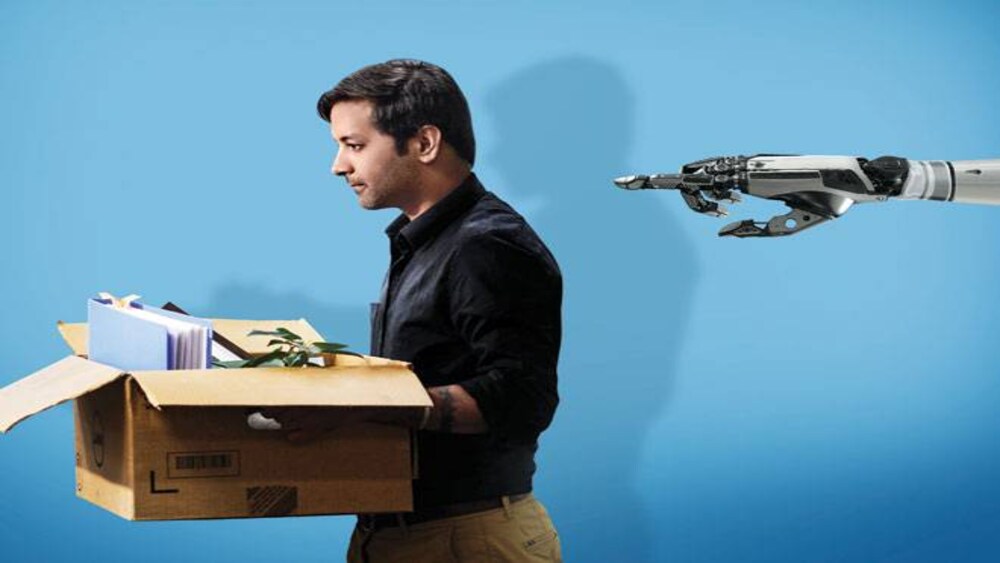
It's like a large server. Except that the grey and orange box has a camera on top and another at the bottom. It screeches, almost as if to say 'I'm working'. One camera reads the route as it suddenly moves sideways and then springs forward a few metres before parking below a rack that can hold up to 500 kg of raw materials, finished goods and parcels. Another screech and it's ready to advance along the rack. In large warehouses, it can move racks at two metres a second.
The box is a robot, part of a storage and order picking system for warehouses that Gurgaon-based start-up GreyOrange has developed. A large e-commerce warehouse can employ up to 200 such robots, called Butlers. They can swarm around like bees for 24 hours without tiring; when low on battery, they automatically dock at a charging station. It takes 30 minutes to charge, or roughly the time humans take for a lunch break.
A warehouse no longer needs men to push trolleys. The server that controls the robot analyses, re-slots the racks and audits inventory "dynamically". One Butler can replace more than one human - a corporate video from the company says the system can result in a 60-80 per cent reduction in manpower. GreyOrange's robots have already been deployed in the warehouses of Flipkart, DTDC, Mahindra, Delhivery, and Aramex, among others. The start-up has moved on - besides e-commerce warehouses, it is now automating manufacturing companies as well. Often, where a Butler's job ends, other robots take over. They can pick the raw material from racks and feed it to machines, doing away with the need for many semi-skilled shop floor workers.
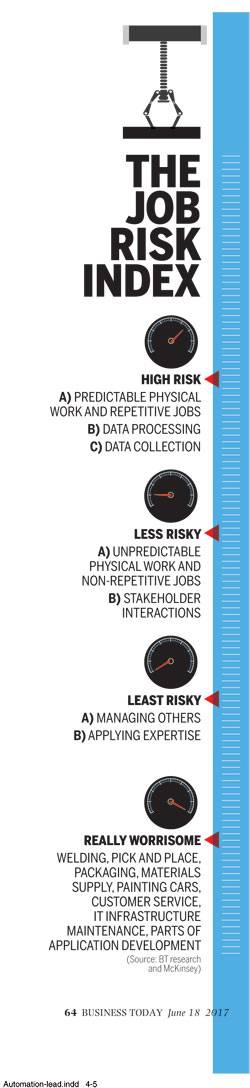
At Honda's new scooter plant at Vithalapur, 80 kms from Ahmedabad, the thunder from its press machines is near deafening. Five giant robots, bought from ABB, orchestrate operations instead of men. Two of them lunge forward, sense metal sheets, pick them up before placing them onto the press that shapes scooter fuel tank frames. The third and fourth robots collect the shaped metal, twist, and feed a second press where the shape is trimmed. And the fifth picks the finished frame and pushes it onto a table. The press shop today produces 4,500 fuel tank frames in 16 hours and 8,200 components overall.
Only 14 people work here in two shifts. Without robots, a manual press shop of this magnitude would have required 72 men. The Vithalapur factory, Honda's fourth two-wheeler plant in India, is one of the most automated in the world. The company's first plant in Manesar has 65 automation processes; the fourth has 241. While Manesar requires one person to produce one vehicle, Vithalapur does it with 0.64 - that's a 36 per cent jump in productivity. A similar script is being written in many green-field manufacturing plants across the country. Everywhere, it is about doing more with less - less people.
That's because price realisation is a challenge. There are only two levers to retain margins on a product: cost reduction or increase in the product price. Price increase is limited, thanks to competition. Manufacturers across the world, and in India, are therefore resorting to an unparalleled use of technology to flatten costs. The fallout, in almost every case, is "technological unemployment", a term popularised by economist John Maynard Keynes in the 1930s.
This term, strangely, is still valid. However, unlike the 1930s, the technological unemployment of this decade is likely to be of a far serious order, and one that cuts across every conceivable sector - from e-commerce and manufacturing to banking, agriculture as well as IT services and BPO.Think of software engineers. Knowing how to code has been the surest way of securing a good life for Indians over the past two decades. In fact, some states such as Andhra Pradesh have an oversupply of engineering colleges. But the advent of Artificial Intelligence, or AI, has meant that machines can now be trained to carry out many standardised tasks software engineers do. Likewise, think of drones that can spray pesticides across farms or identify sick plants that need attention, doing away with the need for labour. Or take condominiums where hi-tech entry systems reduce the need for security guards. Or driverless cars of the future that can hit the livelihoods of professional drivers. Or machines to make pizzas or burgers, because the process is repetitive, just like manufacturing a car.
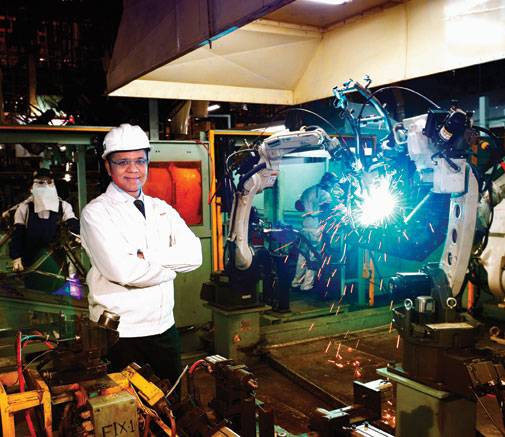
Momentum Machines, a San Francisco-based 'collective of foodies and engineers' claims to have built a robot that can make gourmet burgers without human intervention. In an era where economies are so 'coupled', it takes little time for technologies to cross borders. The job crisis is for real and it raises several uncomfortable questions. How many jobs will the present era of technology unemployment vaporise in India? Will it impact just the bottom-of-the-pyramid employees or also middle-level workers? Can technology replace the highly-skilled? If the composition of employment changes in one industry, will those employees find jobs elsewhere? And what must India do to mitigate the risks associated with high unemployment? Turns out, there are no easy answers.
Question 1: Doomsday?
Estimates of job losses in India because of technology ranges from a doomsday scenario to a more conservative number. Nevertheless, it is not just an Indian problem. Technological unemployment has gripped every economy. So much so that Bill Gates recently suggested that robots should be taxed to stem the progress of automation. While European lawmakers rejected a proposal to impose a robot tax in February this year, it did want a legislation to regulate robots. The World Bank estimates that an average of 57 per cent of jobs in member countries of the Organization for Economic Co-operation and Development (OECD) are at risk because of automation. India is at a higher risk.
In a speech in October 2016, World Bank President Jim Yong Kim said that the traditional economic path from productive agriculture to light manufacturing and then to large-scale industrialisation may not be possible for all developing countries. "Research based on World Bank data has predicted that the proportion of jobs threatened by automation is 69 per cent in India, 77 per cent in China and as high as 85 per cent in Ethiopia." Pankaj Bansal, Co-Founder and CEO of PeopleStrong, says all high-transaction and labour-intensive jobs will take a hit as automation adoption increases. "There will be a visible change in the next three to four years; the first major effect will be seen in manufacturing, IT and ITES, security services and agriculture. We predict that by 2021, four out of every ten jobs globally would be lost because of automation. And of these, one in every four, will be from India," he says.
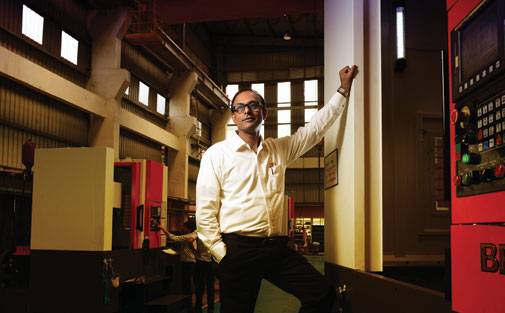
Mohandas Pai, Chairman of Manipal Global Education Services and Aarin Capital, has his own estimate. "If a country grows at 8 per cent, the typical productivity improvement for the labour market is 1-1.5 per cent at most. In India, jobs could grow 6.5 per cent if India grows at 8 per cent. That is in normal circumstances. Now with automation, the 6.5 per cent may slip to 4 per cent. There will be jobs, but the job intensity will come down per unit of growth." Pai rubbishes the claim that a majority of IT jobs will disappear due to automation.
"It is a far cry," he says. "The industry is still growing, but the pace is changing. The people intensity of the work outsourced will come down." If the IT industry grows at 7-9 per cent, workforce addition will be 3-5 per cent. In earlier years, if the industry grew at 9 per cent, jobs, too, would have grown at the same rate, he adds.Manufacturers setting up new plants are employing far less labour. In GE's multi-modal factory at Chakan, near Pune, 550 people produce output of nearly half a billion dollars currently. It is targeting to double that over the next two years.
"We will add people around specialised skills. But it will not increase at the same level as volume. People needs might go up 25-30 per cent to achieve the $1 billion," says Amit Kumar, Director, Global Supply Chain of GE South Asia. A lower rate of job growth or job loss, in both manufacturing and services, may have serious implications on wages. In the IT services industry, freshers haven't seen a salary rise in seven years - it has been ranging between Rs 3.25 lakh to Rs3.45 lakh annually. With excess supply and automation of lower-level jobs, wages are unlikely to rise going ahead. The bigger concern for the political establishment would be lesser job opportunities for the semi-skilled. India already has a high rate of unemployment, and further technology unemployment could only heighten social tensions and agitations by the Gujjars, Jats and Patels vying for government jobs.
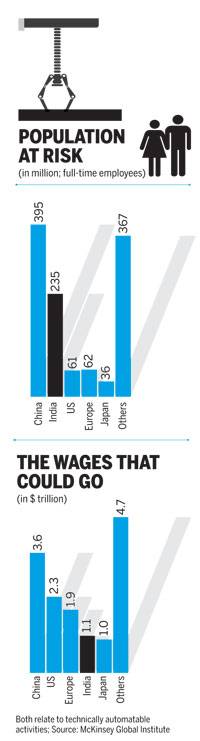
"Of the 2.5 crore babies born 21 years ago, 10 lakh may have died before the age of 5. So there are 2.4 crore who are 21 years old. Of that, 30 per cent may go to agriculture, or marry, and drop out. The rest want jobs," says Pai. "So we need 1.6 crore jobs every year. About 55 lakh jobs are being generated in the country. So one crore people don't have jobs each year for the past 10 years. You have 10 crore people without jobs in the age group of 21-32. If this continues at the same level for the next 10 years, we will have 20 crore people in the age group of 21-45 without jobs or in bad jobs by 2027," he estimates. "So there is no demographic dividend in this country, only a demographic disaster."
Question 2: Skilled.But are they safe?
Keshav R. Murugesh is the Group CEO of WNS Global Services, a business process management firm. Over the years, Murugesh has proved many pundits wrong - some of whom predicted the death of India's BPO industry and a few who said WNS had no future. The company, nevertheless, has consistently grown from $474 million in top line in 2012 to $603 million in fiscal 2016. However, the companys headcount may be growing slower. Five years back, the people growth at his firm would have mimicked the topline growth. "That is the impact of automation," Murugesh says. The company has been investing in robotic process automation (RPA), or software that apes the activity of humans in simple repeatable tasks. BPOs, including WNS, carry out revenue audits for airlines. Passengers might choose two different airlines for two sectors, but the ticket coupon could still be with the first airline since both are partners of the Oneworld Alliance.
In such a situation, an audit ensured that airlines got their fair share of revenues. But this task involved employing "hundreds of employees" for each airline to manually look through all the tickets. Four years back, WNS created an automated tool, took the "data dump" from an airline and fed it to the tool. What took three months to complete, now takes an hour. Smart algorithms throw up a list of suspicious transactions which might need manual intervention, but at a much smaller scale. The larger point: automated systems here have replaced educated and skilled employees.
The advent of RPA, together with the growth of cognitive automation - where advanced algorithms enable decision making - are now hampering the creation of well-paying jobs. In the services sector, which employs many more people than manufacturing, software bots may just about inflict a greater degree of damage. Bots can self-learn and become more intelligent over time replacing people in services such as infrastructure maintenance, parts of application development and maintenance, besides BPO. In the near future, data centres can also look like a de-peopled factory shopfloor.
Technology companies are investing in self-healing networks and systems. A few years ago, Cisco introduced its Application Centric Infrastructure (ACI). Any IT system has infrastructure and applications that run on it. The company built a 'controller' layer in the middle; business policies were built into this controller. "Based on the application, the controller sends the right messaging to the infrastructure to dynamically tune-in, or to dynamically heal if it's broken, so that the application does not see the pain of infrastructure changes, and outages," says V.C. Gopalratnam, Senior VP, IT, and CIO - International, of Cisco.
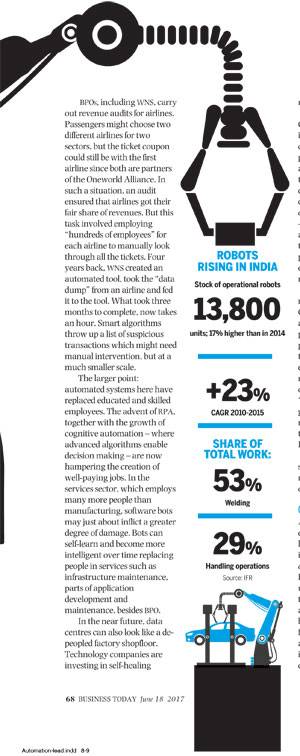
Cisco runs about 2,000 applications in-house and all of these are being migrated to ACI. Clearly, a self-healing infrastructure needs fewer people to maintain it. System administrators, network engineers, database administrators - well paying middle-level jobs - would be redundant, going ahead. Recent reports suggested that Infosys "released" or reoriented about 9,000 employees in the past year and Cognizant is about to retrench 6,000 because of automation of lower-level jobs. Some of these are performance-based eliminations, but automation has played a part (Cognizant said the numbers reported in the media were "vastly exaggerated").
Large-scale elimination of lower-level jobs isn't good news for the mid-level either. If there are less people in an organisation, one would require far less managers. "Those who have built their careers managing people get impacted because there are lesser teams to manage. People with 10-12 years of experience need to roll up their sleeves," says Padmaja Alaganandan, People and Organisation Leader at PwC India. Cognizant, in fact, floated a voluntary separation scheme for senior employees in May, which it said was related to its "overall company strategy to accelerate our shift to digital".
Question 3: The Luddite fallacy Debunked?
A. Didar Singh, is a former bureaucrat, a strategy expert in e-commerce, trade and migration. He also loves his golf. Currently, he is the Secretary General of industry body FICCI. He hands over the book Economy of Jobs to this writer as soon he enters his office. However, his views on automation and technological unemployment are guarded. "We must understand that the competitiveness of Indian industry is based on a large number of factors wherein labour plays a very big role. Why should we give up our labour arbitrage for the sake of heavy capital investment required for automation?" he asks. He proceeds to explain a trend in convergence, between the three segments of the economy - manufacturing, services and agriculture.
"In that convergence, if I give up some jobs because of automation to make myself more competitive, I might very well be offering further services sector jobs for the same activity. I might be creating jobs in an alternative environment. We have to look at the ecosystem." That view, which says that technology doesn't kill jobs but only changes the composition of jobs, is called the Luddite fallacy. The Luddites were English textile workers and weavers who destroyed power looms in the 19th century fearing loss of livelihoods. It is also based on economic history. In a 2015 report titled 'Can productivity save the day in an aging world?', the McKinsey Global Institute says that over the past 50 years, productivity and employment have grown in tandem. "In more than 80 per cent of rolling ten-year periods over the past half century, labor productivity and employment have increased at the same time." The same report then quotes a financial disclaimer - past performance is no guarantee of future results.
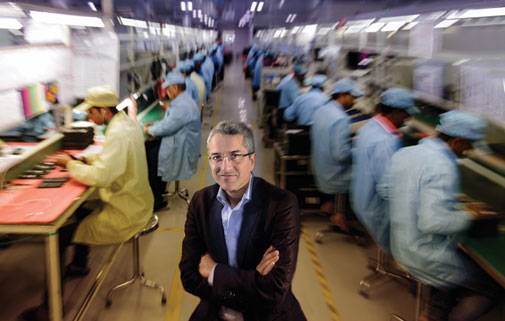
"One concern is that the capacity of manufacturing to be an engine of job growth for emerging economies has declined over time", the report states. Going by CMIE data, Indian manufacturing's share of employment, for instance, as a percentage of people employed in enterprises has slipped from 24 per cent in 1997/98 to 22 per cent in 2011/12. It is highly unlikely that employment in the sector can peak again considering the robotics wave. The past experience may also not apply because almost all sectors of the economy are adopting automation or are on the verge of adopting it. A shop floor worker could have been employed in logistics in earlier years, but the logistics industry itself is banking on technology to improve productivity.
Start-ups such as Bangalore-based Locus use AI to make everything - from dispatching to the routes a trucker takes - much smarter. And service jobs such as maintenance will increasingly become predictive because of development in the Internet of Things. Over the past five years, high computing ability at low costs has spurred many new innovations around automation. "Now, the quality of skills required for running the next generation of automation is different. And if 20 new jobs are being created, 50 are being replaced. So the arithmetic is negative in a big way for the first time. Even in India, we are hearing of automobile manufacturers looking at jobless shop floors," says Pradeep Bhargava, who is on the board of several companies including Cummins India, Torrent Pharmaceuticals, Persistent, and Rajkumar Forge.
India does have a labour cost advantage versus other BRICS countries. A whitepaper from the BRICS Skill Development Working Group pegs India's hourly compensation cost in manufacturing at $1.9 versus $11.9 in Brazil, $2.5 in Russia, $6.4 in China and $5.8 in South Africa. Nevertheless, the costs of managing labour have been rising sharply in many parts of India.B.C. Prabhakar, President of the Karnataka Employers Association, studied 40 wage settlements made between 2016/17 in the state.
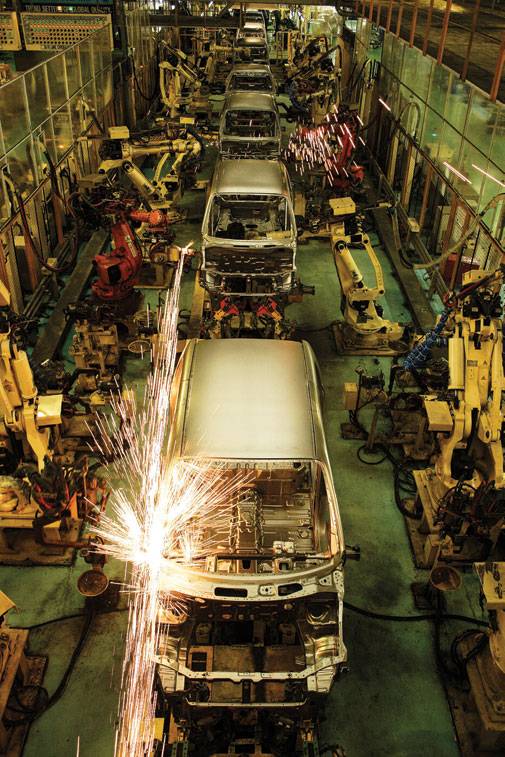
Most settlements, in 21 industries, were for three years wherein over 75 per cent had retrospective effect for a six-to-15-month period. "This indicates the hurdles in agreeing to settle fast. The IR climate would have been in struggle during these period, incurring lots of stress, discomfort, instability and some leading to unrest," he says. The average gross increase in three-year settlements ranged from Rs8,000 to Rs18,000.
In February this year, Bosch Limited reached an agreement with 261 temporary workmen at the company's Adugodi factory in Bangalore. While sources said they were terminated because of automation, Bosch clarified that "in 2015, the plant's operations was severely affected due to business slowdown in some segments. Additionally, change in product mix owing to legislative mandates pertaining to emission norms also mandated changes." Whatever the reason, it proved to be one of the most expensive settlements in the state. Initially, Bosch paid the terminated workers Rs1 lakh each as settlement amount, but after worker protests and state government intervention, decided to pay an additional Rs14 lakh.
Compare the "headaches" of managing labour, rising wages, and settlements to the falling cost of automation, and a business case for higher robotics becomes less fuzzy. India still has a low robot density. Shripad Ranade, Practice Head of Automotive, Engineering & Infrastructure at TATA Strategic Management Group, says that robot density for the automotive sector in India was at 27-29 per 10,000 employees in 2013 and has grown to 30-35 now.
In China, it is about 10-times that number. However, the emergence of low-cost robots with a quicker payback period will accelerate adoption. "Robots did not cost less than Rs10-15 lakh; now, they cost Rs5 lakh. They will not be as good but they will be better than having no robotics," he says. "Manufacturers will consider installing lower-cost robots with a payback period of two to three years compared to expensive ones that have a payback of six to seven years," he adds. "It is possible to calculate ROI even for expensive robots. A robot with high specifications can replace a skilled worker, rather than a semi-skilled one.
Even if the robot is more expensive, it becomes viable because you are replacing higher labour cost." Robotics was once the playground of large manufacturers. But now companies such as TAL Manufacturing Solutions Limited, a subsidiary of TATA Motors, has developed a low-cost robot, BRABO, specifically for small and medium enterprises and has also tied up with Tata Capital for finance schemes. Yatin Tambe runs Friction Welding Technologies in Pune. His company, which has a turnover of Rs4.5 crore, makes components for Volkswagen's Polo and Vento cars. He recently bought a TAL robot. The robot now friction-welds two different components, a process that was done manually earlier. "If humans have to weld about 1,000 numbers a shift, it's boring, and the efficiency of labour goes down after lunch. There is fatigue, too," he says on phone. "So we outsourced that job to the robot."
Question 4: What must India do?
The meeting with Andreas Wolf, Joint Managing Director of Bosch Limited, India, is over strong black coffee at 8 a.m. in his Bangalore office. He doesn't take much time to get into Industry 4.0. After all, Germany (Wolf is German) developed the concept of Industry 4.0. "There is a nice comparison made by an expert from Stuttgart," Wolf says. "In Industry 1.0 and Industry 2.0, the operator was like a commander. He managed everything, the machines, the cutting tool and so on. In Industry 3.0, the operator was like the captain because he told the machine, 'I want you to do this using this software'.
In Industry 4.0, the operator is like a conductor, communicating to the machine. The machine talks to him and uses the data to improve the process."But being a conductor isn't that easy. It requires a deep understanding of both new technology and of the process. "It would require a new style of collaboration because the IT guy has no idea how the process works. In the assembly process, for example, the assembly guy knows exactly how this operation works but he has no idea about the IT equipment," Wolf says. "They have to come together and use statistical methods in the process. This means all shop floor workers have to now qualify to work as conductors. We might have less number of shop floor workers in the future, but we need people with higher qualifications." Wolf is referring to the period of adjustment India would go through before the current generation of workers could be retrained or up-skilled. How long that adjustment would take is anybody's guess. The best case scenario, this writer gathered during the reportage, was 10 years. Bosch, in India, has started training its workers and suggests a top-down approach.
"We will start with the leadership. Why do we need to train our leaders?" Wolf asks and answers himself, "Because our leaders are from older generations who have not been brought up with all the nice stuff such as smartphones, Twitter or Facebook. If the leaders don't understand this, they will not support it." Gearing up organisations and their leadership is just the beginning. The tougher task would be to skill prospective employees. That education, experts say, should begin at ITIs, or even before.
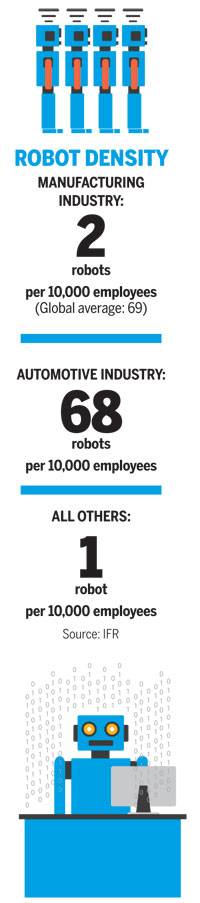
More courses on robotics, 3D printing, machining, mechatronics, or technology combining electronics and mechanical engineering, are the need of the hour at least in the manufacturing sector. "We need people who can manage, maintain and monitor machines; not people who can work on it. The learning ability has to completely change. The job profiles are going to change," says Sandeep Maini, Chairman of Maini Group. The company's interests are diverse, from high-precision engineering components, materials handling, warehousing solutions, aerospace to electric vehicles. Over the next five years, Maini says, India has to revamp the ITIs. "Unless you create a paradigm shift, it will be a challenge. The minimum level of education must increase. Second, those who are not studying beyond Class X, will have no jobs left." This is what scares Mohandas Pai, too. "India doesn't have the foggiest idea of what is happening," he quips. India requires a vision to handle automation. "We are going through a bulge where the largest number of people are going to enter the workforce over the next five years. We are peaking.
Now, with the threat of automation, we are in a mess," he says. "The biggest challenge is middle India - Bihar, UP, MP and West Bengal - which has lesser industries and infrastructure, but more and more people joining the workforce. The strategy should be to promote more labour-intensive industries in these regions, like garment and textiles, electronics assembly, toys, infrastructure and housing."Pai also suggests a change in the country's incentive structure to support sectors with the potential to employ more, and industrial policies that incentivise jobs, more than capital. However, aligning everything India needs to do - relooking tax structures, promoting labour-intensive industries where there is low risk of automation, skilling people, and reforming its vocational institutes - appears to be a tall order. But when Damocles' sword hangs over the country's head, even a small start, somewhere, can be encouraging.
@Goutam20