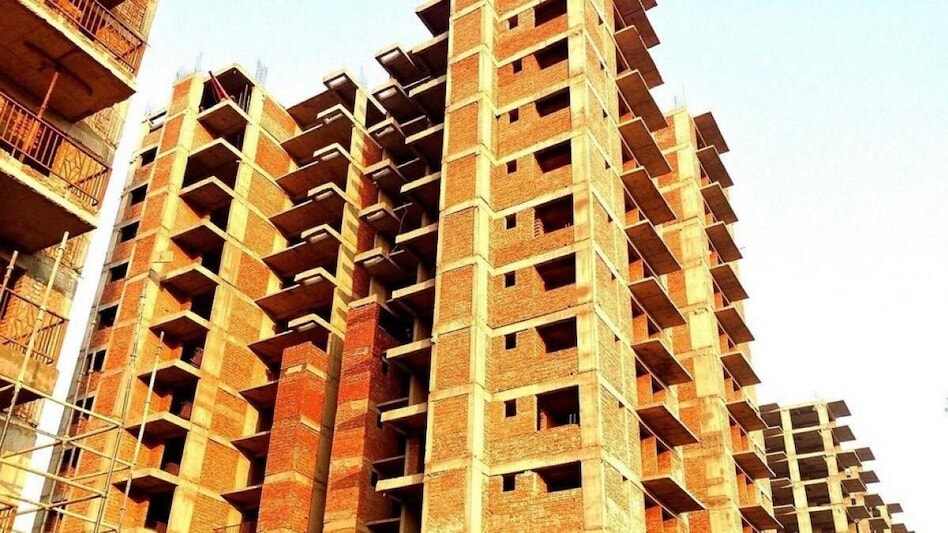
India is on a challenging mission by setting an ambitious net zero emissions by 2070, which was one of the most important announcements at COP26. With India’s G20 leadership until November this year, it has been prioritising energy and climate change mitigation schems to achieve its goal under its slogan 'one earth, one family, one future'.
But at the core, India needs a lot of infrastructure for the transition. The construction industry itself accounts for around 20 per cent of India's annual carbon emissions. This is where climate adaptation becomes critical. With the adoption of sustainable and alternative construction materials, India can cut down carbon emissions to a great extent, said Vikramjiet Roy, MD, Maccaferri India.
Explaining the difference between the conventional ways of construction and sustainable construction, Roy said the conventional ways release particulate material (PM) in the air, discharge excessive heat into the atmosphere, and cause wastage and pollution of water. On the other hand, sustainable construction practices along the alternate construction materials like geosythetics (geocomposites, geogrids, bio materials, geo mattresses) can curb carbon emissions up to 50 per cent , reduce wastage, consume less energy, and address the inefficiencies at building sites. Today, advanced technologies are empowering civil engineering to construct sustainable structures, he said.
Sustainable solutions for various construction needs, such as basal reinforcement, erosion control, hydraulic works, drainage structures, coastal, marine structure and pipeline protections, etc., are available for different geographies and weather conditions. "But the crucial strategy is identifying, prioritising, and applying local solutions for local problems. Local materials are the best to create structure in a particular region. It reduces construction costs, saves time and energy in transporting materials, prevents wastage, and lowers carbon footprint. These materials can help in developing structures that can withstand the local weather conditions. The durability is at the power and the maintenance cost is decreased by almost 4X," added Roy.
For instance, in the Udhampur-Srinagar-Baramulla Railway Link (USBRL) connectivity Project, which is constructed roughly a kilometer away from the highest railway bridge in Jammu and Kashmir, the use of alternative material such as tunnel muck has helped reduce carbon emissions by up to 80 per cent while lowering the project costs by 30 per cent.
Over 3 lakh cubic metres of tunnel muck, a waste product of tunnel excavation, is used to reinforced soil (RS) buildings instead of concrete, as is the traditional procedure. The traditional strategy would have been to build a bridge and a reinforced cement concrete (RCC) wall at the same time. Such construction has huge environmental carbon footprints and necessitates deep foundations. According to the information available, conventional construction methods were also rejected because the area's proximity to a train station necessitated a larger space and a deeper foundation, and the location is in a high seismic zone.
"India requires long-term solutions that will be sustainable over conventional solutions. In this project overall carbon emissions have been cut by up to 80 per cent by removing or reducing the usage of conventional construction materials and substituting them with alternative ones. This was made feasible through the use of tunnel muck and a variety of other sustainable measures such as biodegradable goods, ensuring vegetation on these structures, gabions, erosion control techniques, and so on."
Civil engineer sustainable solution provider Maccaferri Environmental Solutions Private Limited (MESPL) is the Indian arm of Italy-based Officine Maccaferri, which entered India in 1998 and commenced manufacturing (2006-07) of steel-oriented products for rockfall protection, slope mitigation, among others. Polymeric products are mostly used in soil or in slopes for providing functions, like either drainage or filtration, separation, and even strength reinforcement.
The company has been providing customised solutions for various projects to Indian Railways, the Ministry of Road Transport and Highways, the Indian Army and a few private companies.