A new old fabric
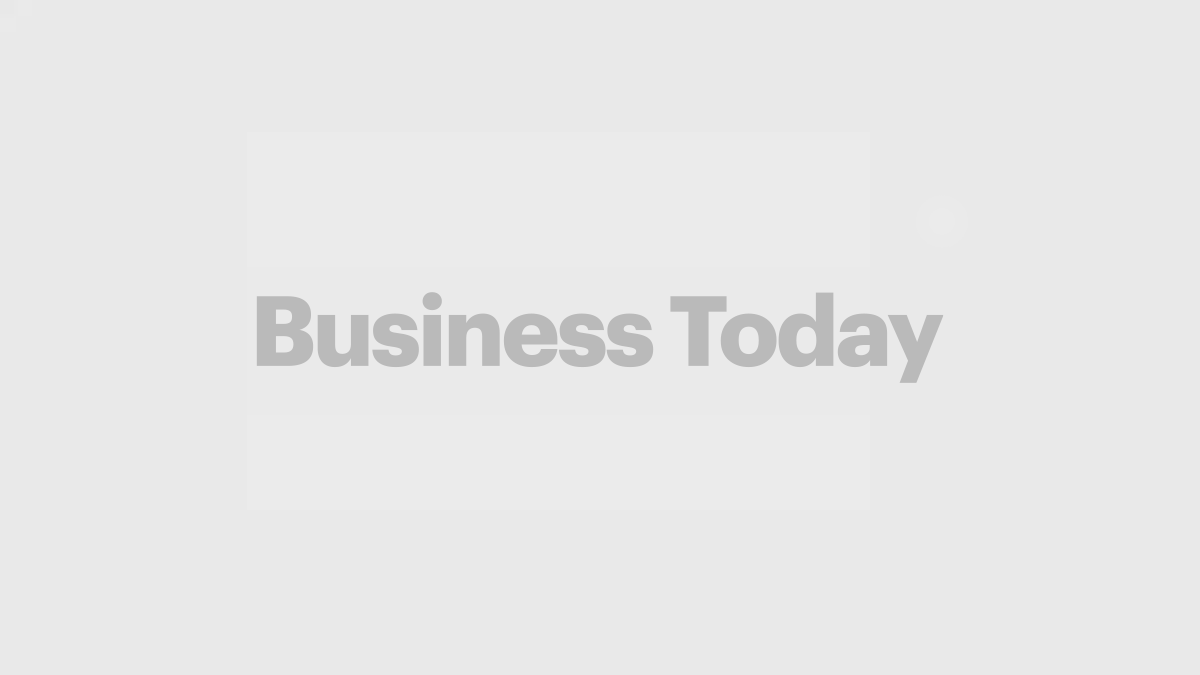
Most tourists give the town a miss even though it probably has monuments that are more ancient than those at Delhi or Agra. But the weavers of Chanderi, a town within a crumbling fort 640 km from Delhi, are not worried about tourism: If the world doesn't come to them, they will reach out by reviving the almost-lost art of the Chanderi sari.
Home to the Bundela Rajputs and Malwa Sultans and later a base for Mahmud Khilji, this town in Madhya Pradesh gets less than 1,000 foreign tourists a year, but its saris, almost as fine as onion skin, are still a prized item in trousseaus of rich Indians.
Although originally made entirely from fine cotton, Chinese silk crept into the warp of the fabric in the 19th century (today, it is Korean silk). It requires weeks of labour by a weaver's family to make one sari, and technology in the form of power looms nearly killed the art with quick imitations.
Almost straddling ancient trade routes passing through central India, but far from markets, Chanderi's weavers had always lost out to middlemen. Today's generation had begun opting out of the weaving tradition. Till that is, Jyotiraditya Scindia, the young Member of Parliament representing Guna, where Chanderi is located, decided to get help to restore the Mughal Fort within which the town is nestled.
Scindia, who the locals call Maharaj, owns a splendid family kothi (mansion) in the fort, once part of his family's domain. As Minister of State for Information Technology and Communications in the first United Progressive Alliance or UPA government, he roped in a nongovernmental organisation, Digital Empowerment Foundation (DEF).
Armed with a grant of Rs 1.5 crore, DEF's Project Chanderiyan is bringing the old and the new together, and has given hope to the young weavers on the verge of quitting.
Chanderiyan is not just about technology. Conceptualised and managed by DEF, it addresses four issues: Preservation of the craft, educating the weavers and their children to tackle the marketplace on their own (which means learning English and tailoring for putting the fabric to newer uses), use of computers in designing, and digitising the archives of the traditional designs.
Chanderi's 3,500 weaver families no longer restrict themselves to just making saris, but will soon learn how to reach out to markets. "We will withdraw in a couple of years after the community becomes self-reliant," says Osama Manzar, Director, DEF.
Step into the Chanderiyan centre inside the restored Raja Mahal within the Mughal Fort, and the change strikes you immediately. This former palace of queens and consorts has become a school for weavers and their families, where they learn how to work out designs with computers.
The time taken to create new designs has shrunk from weeks to days and the library is rapidly growing. "I just keep thinking of new designs all day," says 48-year-old Anwar, now the proud owner of a digitalised portfolio of hand-me-down designs he inherited on paper. His son Furqan has just bagged the order for the official Commonwealth Games scarf's design.
Other classes are on tailoring, block printing and embroidery, so that Chanderi can add value to its traditional sari. Chanderiyan's Director, Shahid Ahmed of DEF, is putting up a portal on which the community will take orders directly and cut out the go-betweens. "The weavers can't access the market directly, so the portal will enable buyers to get them," he says.
"The Planning Commission has already asked us to explore taking the Chanderiyan model to silk weavers in Bihar, Assam and Tamil Nadu," says Manzar. India's handloom weavers turned in produce valued at over Rs 43,000 crore in 2007.
Scindia's plans for market access for Chanderi's weavers are even more ambitious. Currently the Minister of State for Commerce and Industry, he believes Chanderi can make it to the Gwalior-Agra-Jaipur circuit. "The Raja Mahal is now a live monument with potential for community tourism," he beams. "If the weavers can't reach the world, we will bring it here."
Meanwhile, the government has secured GI or geographical indicator protection for Chanderi fabric under the Geographical Indications of Goods (Registration and Protection) Act 1999. Chanderi was the first to get GI protection, which ensures that only saris made here in the distinctive tradition can carry the name Chanderi.
Mohamad Wasim, a 25-year-old weaver at the project centre, and his family used to earn Rs 4,000 per month from its two handlooms till just two months ago. Chanderiyan helped raise it to Rs 7,500. The town produces around Rs 65 crore worth of saris, but 90 per cent of the 3,500 families get around Rs 1,500 each.
But Chanderi's new journey has just begun: The town has 3,500 looms, mostly equipped with the Jacquard punched-card reader, an 18th century device that later formed the basis for programming and data storage media on early computers. Technology has come full circle: Today, it is the personal computer that is turning out designs for the Chanderi.