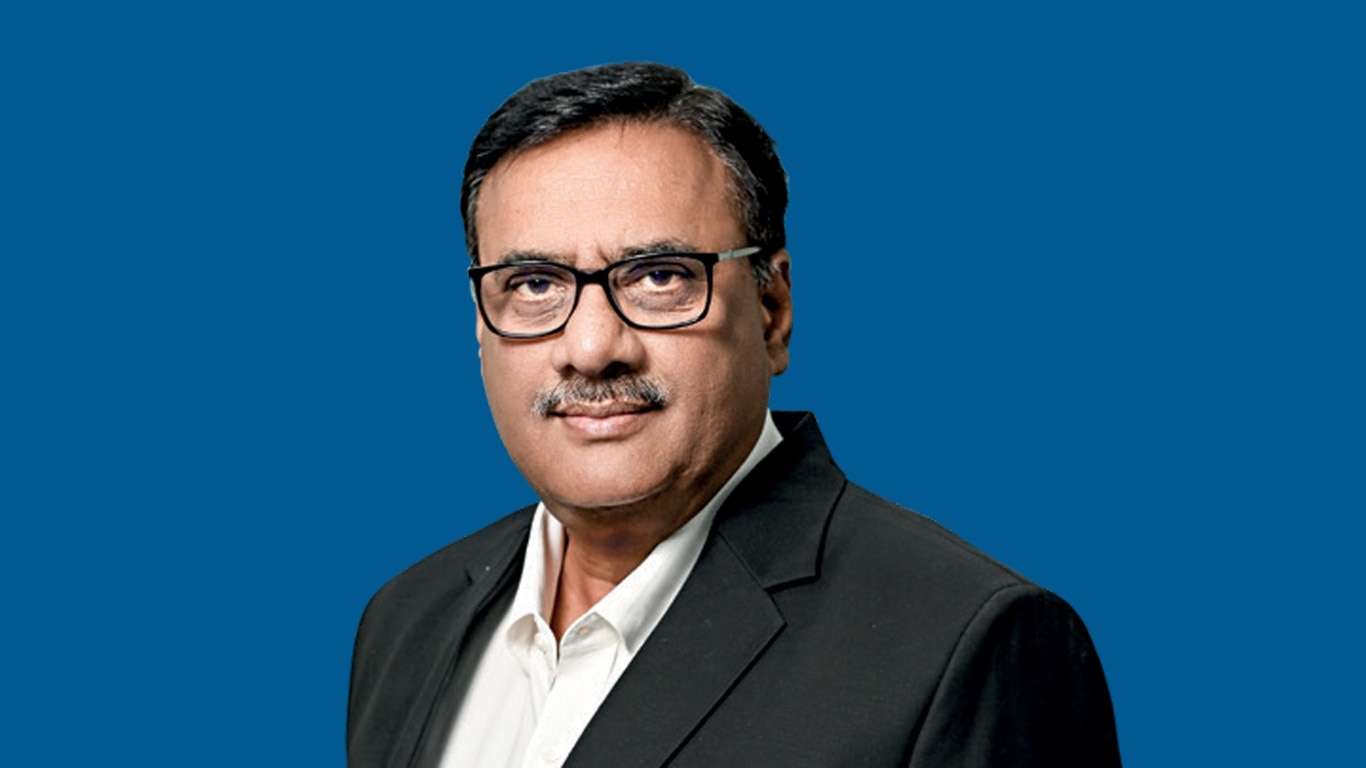
The Indian cement industry is driving positive change
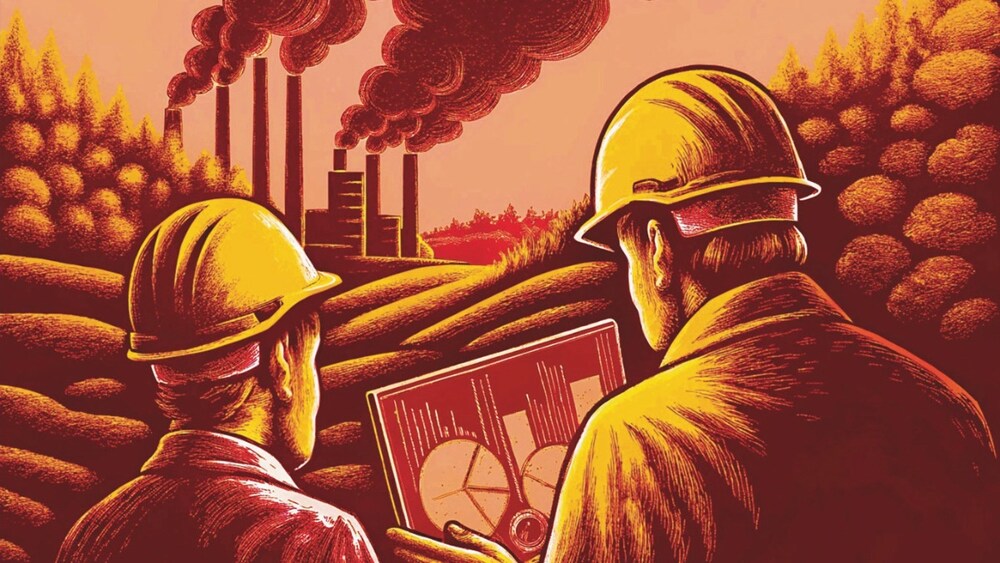
With a greater focus on building a greener future, the cement sector is bracing for greater innovations.
The Indian cement industry, the second largest globally, boasts an installed capacity of approximately 670 million tonnes per annum and a cement production output of around 430 million tonnes in 2023-24. With 175 integrated cement plants and 150 split grinding units across India, it plays a pivotal role in meeting the nation’s infrastructure demands. At the same time, the industry has set ambitious yet pragmatic targets to transition into a greener, more sustainable sector, aligning with the Prime Minister’s vision for India to achieve Net Zero by 2070.
As a significant contributor to global greenhouse gas emissions, the industry carries the responsibility to innovate and adopt sustainable practices. The transformative changes underway go beyond technological advancements-they demand a complete rethinking of traditional processes and a willingness to challenge long-established paradigms. This shift represents a defining moment, not only for the cement industry but also for the broader manufacturing sector.
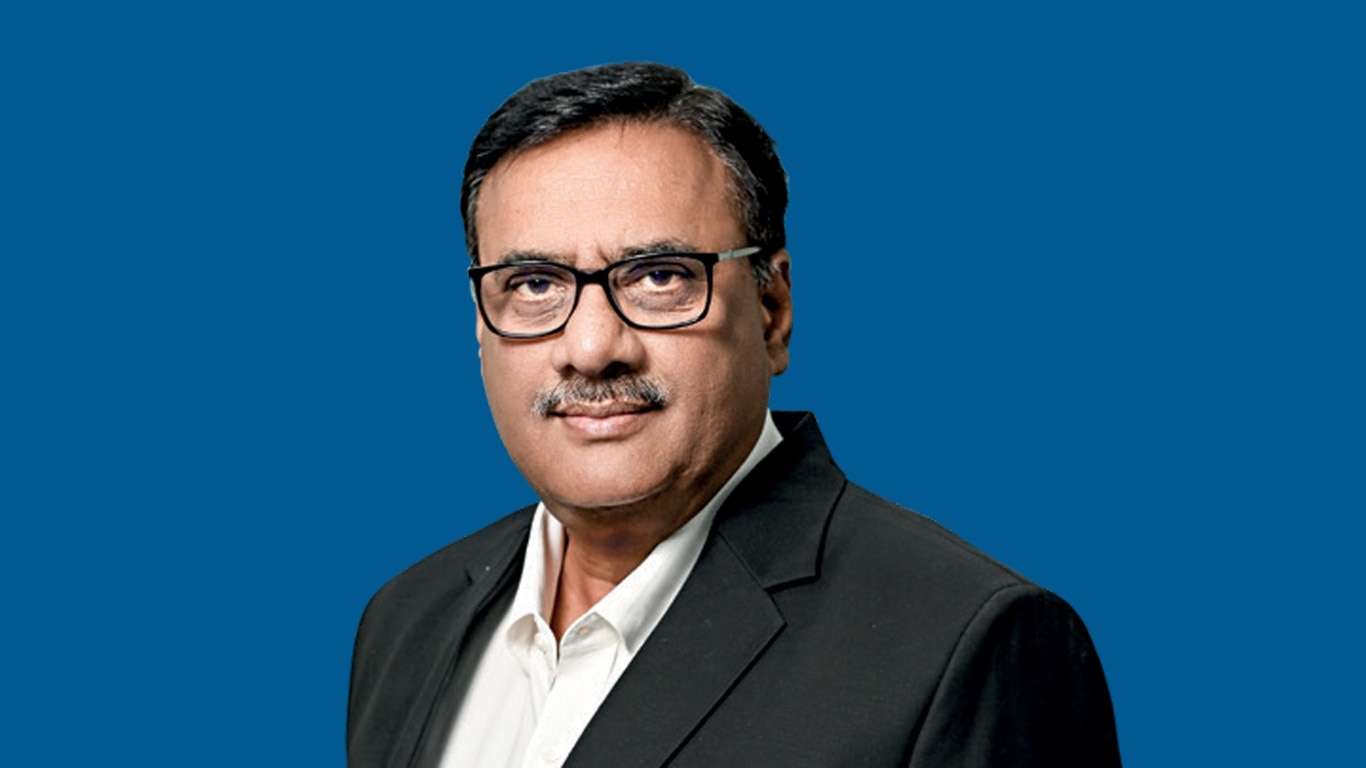
The traditional "take-make-dispose" linear model is gradually being replaced by the regenerative principles of a circular economy. This paradigm shift emphasises the recycling and reuse of products, materials and energy, reducing waste, and enhancing resource efficiency.
The transition is evident. Through concerted efforts, the average thermal substitution rate has reached 7%. A promising fuel that is being explored as a substitute for coal and natural gas for cement kilns is green hydrogen. But we are in the infancy of adopting it widely and require further R&D to bring it as a mainstream solution.
Further, the industry has led the transition to green products by making blended cements using alternative raw materials. The industry has also embraced the use of industrial waste materials, such as fly ash from thermal plants, slag from ferrous and non-ferrous industries, and waste from paper and mineral processing industries. However, a large volume of industrial waste from other sectors-such as red mud from aluminium production and gypsum from thermal and fertiliser industries—remains underutilised. To address this, a national inventory of industrial wastes and by-products could enable the sustainable management of these materials, helping mitigate the depletion of natural limestone reserves. This approach would not only benefit cement manufacturing but also support other industrial applications, fostering a more sustainable and resource-efficient economy.
The sector is also investing heavily in energy efficient technologies, including advanced kiln systems to optimise energy use. Notable progress has been made in the adoption of renewable energy sources, alongside the increasing implementation of waste heat recovery systems (WHRS). WHRS captures waste heat generated by kilns and converts it into usable energy, reducing energy costs and enhancing sustainability. AI and ML are also being integrated to further enhance process efficiency.
Kiln electrification is an emerging concept with the potential to revolutionise decarbonisation efforts. While still in the developmental stage, this technology could drastically reduce CO2 emissions by replacing fossil fuels with electricity-ideally sourced from renewables. This technology has the capability of producing the extreme temperatures required for clinker production using renewable electricity, addressing the thermal emissions that account for around 40% of total clinker-related emissions. Early implementation of pilot projects will be crucial to fully realise the potential of this decarbonisation pathway. However, challenges such as high infrastructure costs and the intermittent availability of renewable energy, highlight the importance of advancements in energy storage solutions to make kiln electrification a viable and scalable solution.
To address the remaining 60% of clinker-related emissions from cement manufacturing, a technology being considered is Carbon Capture, Utilisation, and Storage (CCUS). If it is scaled correctly, it could significantly reduce the overall carbon footprint. Supportive policies, incentives and regulatory frameworks can stimulate investment in CCUS infrastructure and research, fostering innovation and technological development. Additionally, government-led initiatives can facilitate the establishment of a CCUS value chain, providing seamless linkage from capture to utilisation and storage of carbon.
Logistics costs account for nearly 30% of the total manufacturing expenses in cement production, making it a critical area for innovation and optimisation. To address this, the industry is increasingly moving towards more environmentally friendly options such as CNG/LNG and electric-powered trucks, waterways and railways, reducing reliance on traditional road transport.
Over the last decade, sustainability topics have transitioned from being aspirational goals to becoming non-negotiable imperatives, largely driven by growing customer expectations, government regulations, and stakeholder demands. Achieving these goals demands industry-wide cooperation, bold action encompassing technological innovation, investment in R&D, process optimisation and the development of sustainable materials.
The road ahead is not easy, yet the cement industry is in an excellent position to drive positive change through innovation, green energy integration and sustainable manufacturing practices to shape a future where economic prosperity coexists harmoniously with environmental stewardship.
Views are personal. The author is Neeraj Akhoury, MD, Shree Cement