Moving From Assembly to Manufacturing Base
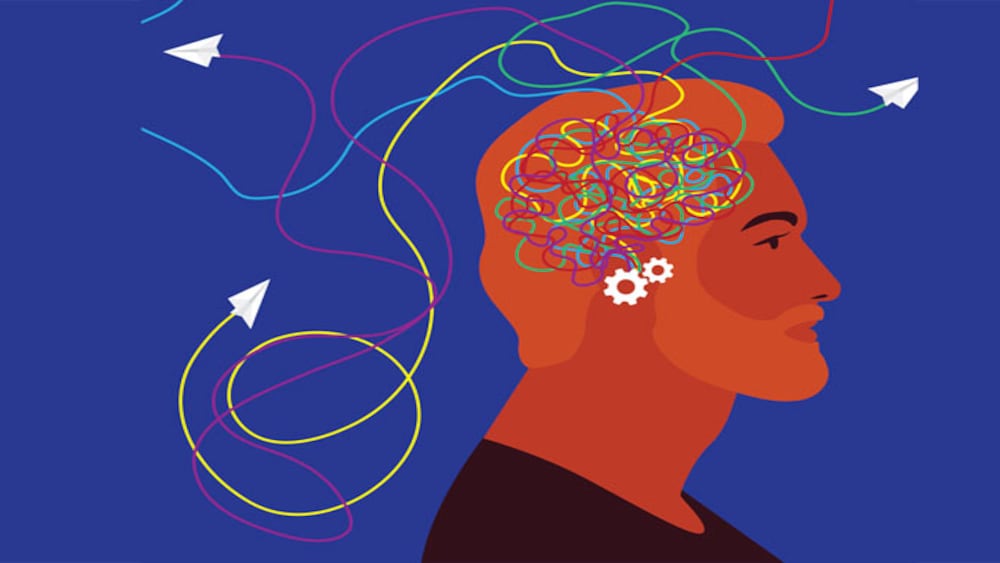
If you were to ask me, what is the one thing that's critical to drive the Atma Nirbhar Bharat agenda for the electronics industry, component manufacturing ecosystem will sit right on top. To drive the key tenets of Atma Nirbhar Bharat, from the Appliances, Consumer Electronics (ACE) or the electronics industry's perspective, component manufacturing becomes the bedrock of the ecosystem. The market size of India's ACE industry was Rs 76,400 crore ($10.93 billion) in 2019. It is expected to double to reach Rs 1.48 lakh crore ($21.18 billion) by 2025. Component manufacturing not only gives the necessary impetus to the industry, but also provides a major boost to the economy at large. Reduced dependencies on import lead to greater demand for Make-in-India and employment generation, including training and skilling India.
Opportunities And Challenges
Looking at the current manufacturing economies in Asia, it has taken decades for the industry and the government to reach the current levels. From establishing a supply chain to achieving economies of scale in manufacturing, it has been a journey of discovery for China and other South East Asian countries. If I have to take Panasonic's example, we have been running manufacturing operations in Thailand and Malaysia for several decades and are exporting air conditioners from there to more than 50 countries.
India's demography, manufacturing, and trade landscapes differ significantly compared to other countries and hence, opportunities and challenges go hand-in-hand. The sector does have challenges related to domestic supply chain, high cost of finance and limited design capabilities. Also, our journey to building India as a manufacturing hub is new compared to the rest.
But I believe the time is ripe and we are seeing an explosion of demand and with new-age technology, we can traverse this road faster and catch up with our competitors. With IoT-based systems and the phygital economy, this is India's moment to position itself for many decades to come.
A Self Reliant India
We know our challenges and understand the opportunity. We also know which levers to press to bridge our disabilities. I have a clear three-step strategy to catapult India into a manufacturing economy and all the three steps need to be undertaken simultaneously.
? Unlocking manufacturing demand - Through a holistic approach considering the phased manufacturing programme. We have already made significant strides in terms of building demand-and-supply pipelines. To encourage local manufacturing and assembly, policy changes have been announced in every Budget in the last few years. From duty on components and finished goods to reduction in GST for smaller-size TVs to fuelling local demand in smaller towns, all these steps encourage Make in India. While this is a step in the right direction, it is not enough as it drives only local assembly, which will not lead to 100 per cent manufacturing in India. And this brings me to my next step.
? Backward integration of supply chains - The success of Indian manufacturing relies on backward integration of supply chains and expanding their capabilities. Based on my experience for close to three decades with several industry positions, I do believe that we can increase the potential of the electronics sector multi-fold by 2025, with backward integration and localisation because of the success of PCBAs, PCBs, and ATMPs. For the uninitiated PCB or, Printed Circuit Board, which is used across IT electronics, consumer electronics, auto, industrial electronics, auto, LED lighting, medical electronics, and mobile phones, is a $47-billion opportunity (PCB Assembly - close to $38 billion and PCB - close to $9 billion). ATMPs (Assembly, Testing, Marking, and Packaging) of the electronic components itself is a $10-billion opportunity. With the rise in demand for electronic devices, there will be increased demand for components as well. To sum up, Indian electronic manufacturing companies can propel towards greater success with a few fundamental tweaks in the industry. It has the potential to increase local output since it targets efficiency and should generate more demand by keeping a check on the price. A benchmark example of why backward integration in manufacturing works is that of the automotive industry in India.
? Opening up exports - It is important to explore new geographies for expanding the demand base through export. Here we need to concentrate on categories where we have inherent strength. To succeed here, we need to explore unique business models, which may not only focus on the export of finished goods.
If you look at the opportunity, a number of western geographies, which are going to be upcoming economies in 15-20 years, can be potential markets for us. We can explore a hub-and-spoke model where India becomes a hub and creates many spokes to cater to assembly requirements and finally service the economy there. Lets look at Egypt as an example - which is well positioned and checks most boxes. India can look at supplying components to them and also service various parts of Europe and Africa from Egypt.
The Manufacturing Story
If we look at the electronics industry, we currently have TVs that are fully assembled in the country. Similarly, for air conditioners, nearly 80 per cent are manufactured or assembled in India. And the recent prohibition of importing air conditioner with refrigerants has encouraged local assembly of the balance 20-25 per cent, which were imported till recently. This summer we will witness 100 per cent of ACs assembled in India.
Technically, we are assembling most of the consumer durables in India itself. Now the next big step is about speeding up backward integration. Lets take the example of the AC industry here. It is around Rs 17,000-18,000 crore, and we have taken a target to take it to Rs 1 lakh crore in 2029 - 65 per cent from domestic demand and 35 per cent from exports. We are minuscule today in terms of exports. With backward integration, we can build components such as motors, compressors, PCBAs, PCB components, aluminum and copper. The possibility of localisation here is in excess of Rs 75,000 crore. Also, it is a high job-intensive division - not only for manufacturing, but through the entire product life cycle with sales, servicing, installation, etc.
Government Measures
The government is proactively taking steps to address disabilities, build an efficient infrastructure, and promote ease of doing business. Policy reforms and notable improvements in the business regulatory framework have had a tremendous impact on the development of India's ability to attract FDI and trade in the manufacturing sector. For instance, the reduction of corporate tax and the introduction of a production-linked incentive (PLI) scheme are the right measures where the country is looking to collaborate with enterprises across levels.
The government introduced the PLI scheme to strengthen domestic manufacturing, increase self-reliance, and reduce import bills. PLI offers incentives to companies on incremental sales from domestically manufactured products. Further, it aims at inviting foreign entities to establish their base in India and encourages local companies to set up or expand existing units. Companies can bring globally integrated manufacturing capabilities for high-value output, thereby, providing higher returns to upstream producers besides employment opportunities. It strategically drives India into key segments of global value chains and makes India self-reliant.
Good Days For Manufacturing
India has all the potential to emerge as the next global manufacturing hub. In times of deep economic crisis, such as the recent Covid-19 pandemic, swift government intervention through strong fiscal response and injection of capital into the economy is necessary.
While the economy as a whole needs significant support, the government and the industry must convert this adversity into an opportunity to strategically invest in high technologies for priority sectors such as energy, electronics, and electrical equipment, including computers, telecommunication, and space. It should inject aggressive economic incentives and review the current business practices to bring in more trade and investments into advanced manufacturing sectors.
(The author is President & CEO, Panasonic India, and Chairperson, FICCI Electronics & White Goods Manufacturing Committee)