At the crossroads
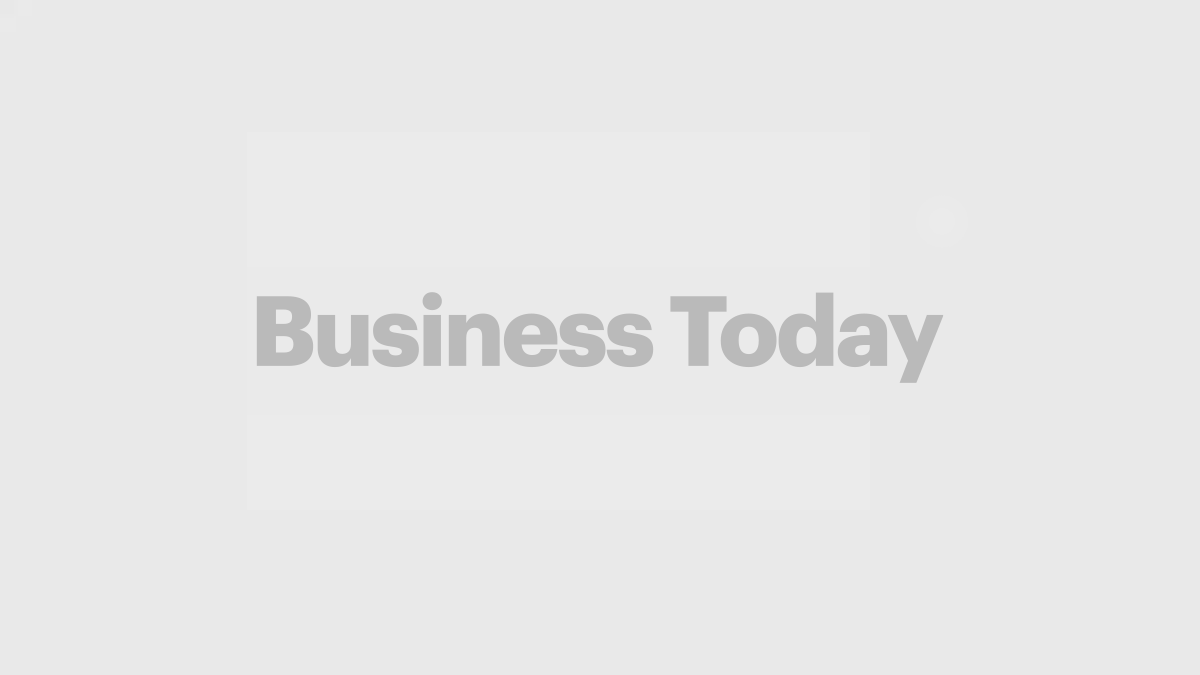
In September, TVS Motors was forced to produce 10,000 fewer bikes (five per cent of its capacity) for want of components. In fact, the shortfall could have been greater if the automaker had not thought of periodically airlifting components from abroad.
But it isn't just TVS Motors where production has been hamstrung by the inability of its vendors to meet all its component requirements. All the major automakers in the country, including Tata Motors, Ashok Leyland, Ford India and Hyundai Motor India, have been struggling to meet the runaway demand for trucks, cars and two-wheelers in the country, which has translated into record sales over the past two months. In August, sales of cars and twowheelers in the country touched an all time-high, growing by 33 per cent and 28 per cent, respectively, while commercial vehicle sales rose by 28 per cent.
So what has led to this mismatch between demand and supply of auto components? Its genesis lies in the way the $30 billion (Rs 1.38 trillion) Indian auto component industry reacted to the global financial crisis of 2008. As the crisis unfolded, demand for components, both within the country and globally, plummeted suddenly, causing volumes to shrink by more than 50 per cent almost overnight. The industry reacted by laying-off people and cutting back production.
"An atmosphere of gloom and doom prevailed and the mood in the industry was clearly pessimistic," says Venu Srinivasan, Chairman, TVS Motors. With the industry fast running out of cash, all expansion plans were put on hold. As a result, investment in fresh capacity grew by just one per cent in 2008-09 as against 33 per cent the previous year.
While the auto component sector was trying to cope with the challenges thrown up by the downturn, it was caught completely off-guard by the quick turnaround in the fortunes of the automobile sector on the back of the government's fiscal stimulus package. By the second half of financial year 2009-10, the commercial vehicle sector had revived.
The stimulus sent a clear signal that the state would not allow the economy to collapse and this shored up the consumer confidence driving up sales of cars and two-wheelers. To meet the surge in demand car majors from across the world rushed to set up new capacity or ramp up existing ones. In the last two years, fresh car production capacity has risen by two million.
Even as all this was happening, the auto component sector was still in the cash conservation mode. And when it did finally change gear and began to push the accelerator, a new set of challenges confronted it. The Tier-II and Tier-III suppliers, especially those in the forging, casting and fabrication industry, who had laid-off skilled and semi-skilled labour, found it difficult to get them back. The bigger players, on their part, were unsure about the sustainability of the stimulus-driven demand and preferred to wait before making fresh investments.
With the component sector failing to cope with the new demand, the auto majors had no option but to resort to imports, which grew from $5.2 billion (Rs 23,920 crore) in 2007-08 to $8.2 billion (Rs 37,720 crore) in 2009-10, a growth of 58 per cent in two years. "This is clearly worrying. Today imports account for almost 30 per cent of the industry demand," says Srivats Ram, President, Automotive Component Manufacturers Association of India (ACMA) and MD, Wheels India.
The auto component sector really needs to worry about this trend, given the future outlook for the industry. According to an ACMA-Ernst & Young study, domestic demand for auto components is expected to jump from $30 billion (Rs 1.38 trillion) in 2009 to $119 billion (Rs 5.57 trillion) in 2020. During this period, exports are expected to rise from $3.8 billion (Rs 17,480 crore) to $29 billion (Rs 1.33 trillion), the industry will add another 1.2 million people to its workforce and its share in the country's GDP will increase from 2.1 per cent to 3.6 per cent.
"We have no choice but to invest in capacity. Take the case of the cars. It took us 60 years to reach a capacity of two million cars. In the next 10 years we will be producing nine million cars. If you do not invest, you will lose market share," says Baba Kalyani, Chairman and Managing Director, Bharat Forge. Adds Ram, "To meet the increase in demand, we need to invest at least $3 billion (Rs 13,800 crore) every year for the next 10 years. In other words, we need to invest in the next five years what we have invested in the last 50 years."
But scaling up would not be easy for the industry since it presents its own set of challenges. "The margin in the industry is wafer thin. While the automobile majors do compensate us for the increase in the cost of raw material, other overheads such as higher power costs, wages, etc. have to be borne by us. This means the industry is left with very little surplus. High interest costs are not very helpful either," says Surinder Kapur, Chairman, Sona Group.
Besides, companies will have to get more competitive and offer more value to the customers through their products to get better margins and invest in expansions, according to Kalyani. They must invest in product development as technology could become a major differentiator in the near future. Then there is the issue of finding adequate skilled labour. Industry should also look at consolidation.
Says Kalyani, "It is one thing to supply for a volume of million cars and another for 10 million cars. Tier-II and Tier-III players have to consolidate or grow bigger. That's the toughest challenge."