Automakers: Tightening the screws
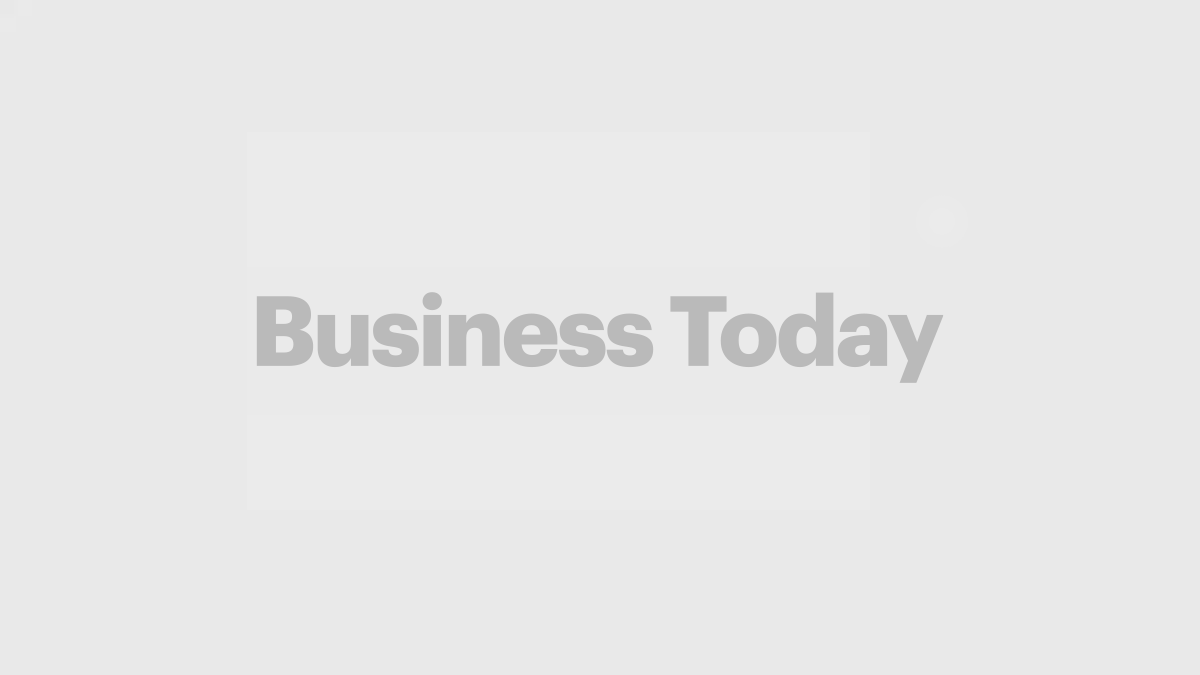
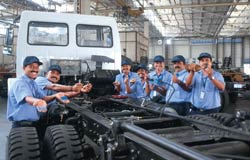
At a time when demand has shrunk, however, increasing production is hardly a priority for the Indian auto sector. But getting more productive certainly is. Data from industry body, Society of Indian Automobile Manufacturers (SIAM), shows that since 2002-03, the sales of all automobiles has risen 13-16 per cent every year, except in 2007-08, when sales fell 4 per cent in volume terms, primarily because two-wheeler sales crashed, even as cars and trucks did show growth. In the current year, however, the plunge has been across the board, with sales volumes (till January) down an overall 4.3 per cent.
Automobiles is a cyclical industry; the last downturn came in 2000-01, although a silver lining at the time was exports. Today, it’s a double whammy: Global demand has slumped thanks to a global liquidity crunch and an increase in financing costs. For auto makers, there’s little option but to embark on a ruthless cost-cutting drive and squeeze out efficiencies from every rupee spent to stay competitive. No stone—not even small ones— are being left unturned: Car-pooling is being encouraged, train travel made compulsory, air travel restricted, hiring of high-end taxis stopped; and a few have also stopped handing out snack packets on the shop floor.
It’s a grim situation out there, with Tata Motors’ highest ever quarterly loss of Rs 263 crore for the quarter ended December 2008 being the biggest manifestation of the rough road. The Rs 6,300-crore commercial vehicle giant has recognised the gravity of the downturn and aims to shave Rs 1,000 crore off its production costs over three years. It is also seeking to reduce the total time of manufacturing by changing some processes and involving vendors at the design and development stage in a bid to cut time and costs.
No more free lunches How auto makers are getting into shape. |
|
Rude Reminder
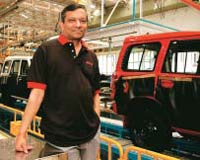
Mahindra & Mahindra |
CAPEX Reduction: |
The Nuts & Bolts
May outsource some operations. Reduced CAPEX outlay by 10 per cent over the next three years. Will shift excess officers from one plant to another.
Number of trips made by senior management brought down by 65 per cent.
Employees not allowed to carry forward privilege leave. Fresh recruitments curtailed. Unfilled positions to be re-approved. |
Other auto majors are also cutting back. Ashok Leyland, the Chennai-based truck manufacturer that has seen a 30 per cent drop in sales so far in 2008-09 and an erosion in operating profit margins during the third quarter, has lowered the estimate of its investments for the next three years—from Rs 3,300 crore to Rs 2,000 crore.
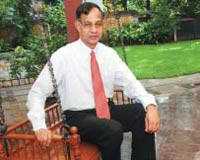
Ashok Leyland Group |
CAPEX Reduction: |
The Nuts & Bolts
Workstations at new production lines have been designed in a way to improve employee efficiency. Use of techniques like Effort and Ergonomic Index (EEI). Speed up clearance of ideas of employees on value-engineering concepts.
Encourage carpooling by senior employees.
Voluntary salary cuts from CEO to lowest level executives. Aim is to reduce wage bill by 20 per cent in the current fiscal. Reduced working days at the plant from six to three. |
Maruti Suzuki, the country’s largest passenger car manufacturer, says similar cost-saving ideas from more than 1 lakh employees have helped the company save Rs 50 crore so far in 2008-09. “We have an internal target of bringing down our production cost by 5 per cent every year and so far, we have achieved the target (this year),” says M.M. Singh, Managing Executive Officer (Production), Maruti Suzuki. The company has adopted a “one gram-one component” philosophy from its Japanese partner Suzuki, whereby shop floor employees attempt to reduce the size of each component of the car without compromising on its functionality.
Bajaj Auto aims to bring down freight and packaging costs for exported vehicles by 20 per cent by the end of 2008-09 by packing two vehicles together and using railways instead of road transport. S. Sridhar, CEO for the two-wheeler segment at Bajaj Auto, claims that since the company brought down its list of suppliers and gave voluntary retirement to around 3,000 employees a few years ago, it doesn’t really have to resort to drastic measures— not yet, at least.
Trying to Improvise
Some like Ashok Leyland are utilising this time to study movement of employees across the shop floor and trying to improvise on their flow of work so that overall productivity increases. For instance, at one of the units in its Hosur plant in Tamil Nadu, managers noted that dash panels were being manually removed to be placed on a pallet. The company was quick to shift to an automated system for this purpose. This has helped improve productivity by 41 per cent for that task. The company has implemented more than 1,500 such ideas generated by employees.
Suppliers of auto components, too, are moving towards adopting leaner cost structures. Delhi-based Subros, the largest manufacturer of car air-conditioning systems, is, in addition to reducing expenditure on travelling and advertising, trying out value engineering ideas to bring down production cost. “After consultation with our auto clients, we have changed our sourcing strategy by shifting import procurement from Japan to other Asian countries,” explains Vice President Pawan Sabharwal. On the shop floor, the company has reduced manual intervention in certain operations and employees are being trained to operate several machines instead of just one kind of machine.
Indeed, many of the belt-tightening measures being adopted by the auto sector may seem extreme— like lights being switched off daily for at least 30 minutes in each department or switching off air-conditioners and lights during lunch hours or extra varieties of lunch being cut or snack packets being stopped for shop floor workers. These may seem small cuts but they all add up—especially when you’re operating on an employee base of tens of thousands.
![]() Ravi Kant | ![]() Baba Kalyani |
Expected cost savings: | Expected cost savings: |
The Nuts & Bolts
Several process improvements initiated to increase productivity. Vendor involvement at early stage for better design and total cost reduction.
Minimise travel costs and optimise the usage of the company’s transit flats.
During plant shutdowns, employees given salary for 50 per cent of working days and the balance adjusted as leave. | The Nuts & Bolts
Rationalisation of production facilities within the plant as well as across locations. Reduction in outsourcing of processes.
Internal deadlines and targets laid out for reducing working capital. Frozen discretionary expenditure such as seminars, conferences, advertisements and consultants.
5-20 per cent reduction in salary across the board, right up to the Chairman. |