Skilling the unskilled
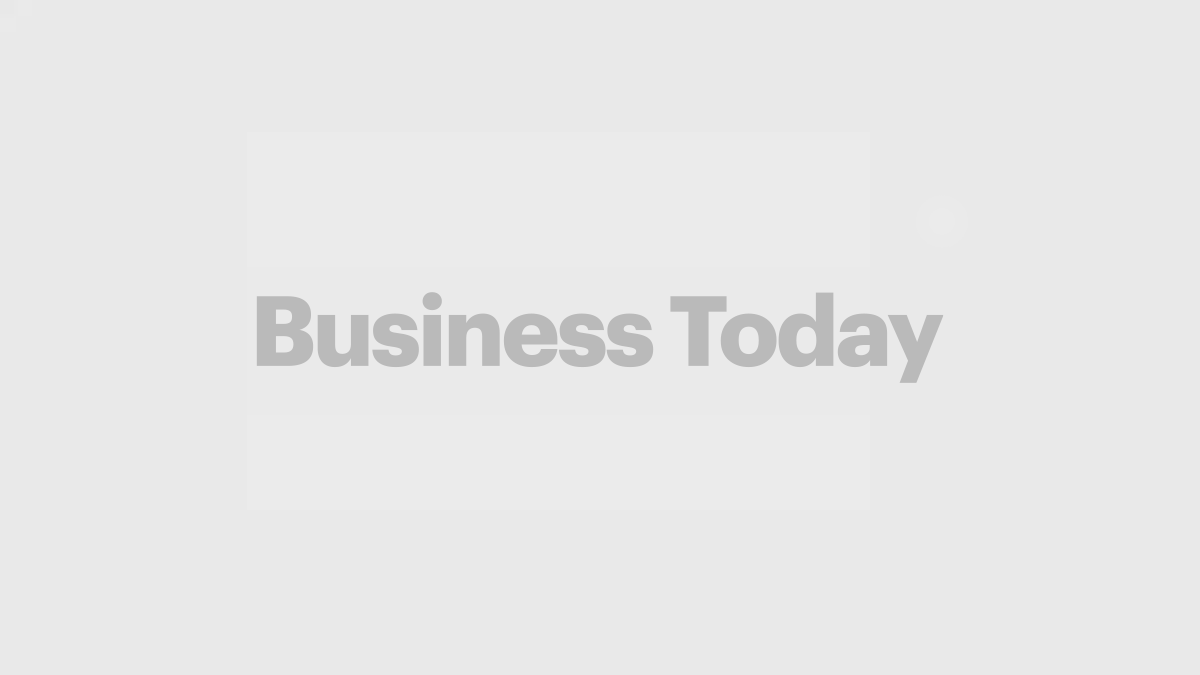
- Six months ago, Kailash Singh, 20, a native of Payyan in Bageshwar district of Uttarakhand, was working as a waiter at a hotel in Almora having somehow completed his senior school (10+2). Today, he handles a piece of equipment worth Rs 5 crore that machines front axle beams at the new manufacturing unit of truck and bus maker Ashok Leyland Ltd (ALL) at Pantnagar in Uttarakhand.
- Twenty-year-old Rashmi Pilakwal's world came crashing down when her father, a small-time farmer in Kaparkhan in Almora district of Uttarakhand, died in 2009. Her family, including her mother, two sisters and a brother, was in deep financial distress. Not anymore, Pilakwal, a 12th class graduate, sends home Rs 3,000 a month from the stipend of Rs 5,500 she earns at ALL.
- Similarly, Mamta Rawat, 20, a Commerce graduate and a native of Ranikhet, supplements her single mother's earnings as a teacher, while Mamta Joshi, 23, married and a graduate belonging to Almora town, supports her husband's family of 10 with her income.
While Singh, Pilakwal and Joshi want to become automobile engineers, Rawat is keen on becoming a management professional. They and 200 others are beneficiaries of a new experiment at ALL's Pantnagar facility that seeks to bridge the divide between unemployment and unemployability and address Indian industry's serious bugbear—lack of skilled labour, especially in the backward districts of the country.
The Gap
State governments offer attractive incentives to draw industries to backward areas to spur their economies. But these incentives come with a condition— a certain percentage (normally 70 per cent) of the employees should be locals. This criterion has proved to be a major problem for the industry—not because they don't want to employ locals, but because of lack of talent in such areas.
Take the case of Uttarakhand: Only three to four per cent of students completing school (10+2) have mathematics as a subject. Also, there are very few technical diploma holders and engineers to meet the needs of industries that have rushed to set up modern manufacturing facilities at places such as Pantnagar. Over time, a paradoxical situation has come to exist—massive unemployment on one hand and acute scarcity of skilled labour on the other. Most companies resort to contract workers to circumvent the government mandated norm.
ALL, which has set up a Rs 1,200-crore fully integrated manufacturing unit at Pantnagar for producing 50,000 trucks a year in the first phase and up to 75,000 units in the second phase, decided to try something different. It opted to convert this challenge into an opportunity for implementing its bold new strategy of setting up an integrated workforce while taking head-on the issue of demand-supply gap in skilled labour.
The idea of an integrated workforce has been occupying the minds of ALL's top management ever since various human resource (HR) surveys revealed that, unlike the executives, the shop floor workers, though well committed in their work, do not buy in 100 per cent the company's vision. Mindset, it was learnt, was the major reason. Shop floor employees felt inferior to the executives as they typically had lesser education and growth opportunities compared to the executives.
Once a workman, always a workman was their grouse. Separate canteens, different uniforms, etc., only reinforced their inferiority complex. "Mission YEs—a movement started to empower young executives in ALL—went into the problem and recommended that we work towards an integrated workforce where there will be no master-servant relationship and all employees, including shop floor workers, enjoy common facilities. More importantly, shop floor workers will have the same opportunities to learn and grow within the organisation as the executives have," says Shekhar Arora, Executive Director (Human Resource), ALL. The management accepted the recommendation and decided to implement it at Uttarakhand facility as it is a new factory without any legacy issues.
Bridging the Divide
Once that decision was made, it gave ALL the flexibility in handling the gap between the skills required by the industry and the actual available skill base. It launched a programme called BLESSING—Building Leaders of Excellence for Social Sustainability through Inspiring & Nurturing Gennext. "The objective of the programme is to enhance the prospects of sons of the soil by empowering them with attitude, skills and knowledge which would qualify them both academically and with hands-on skills to become practising executives and to grow to positions of higher responsibilities in future," explains Arora.
To translate this vision into reality, ALL signed an MoU with NTTF (formerly Nettur Technical Training Foundation)—a premier technical training institution—to offer a four-year certificate programme leading to a Diploma in Manufacturing. The programme works like this: NTTF identifies students for the programme from within Uttarakhand through written tests and interviews.
Candidates have to be 18-25 years of age, have a Class 10 or 12 certificate or a diploma from an Industrial Training Institute, with at least 50 per cent marks. Once selected, they undergo the four-year diploma course at NTTF's educational centre at Pantnagar located inside ALL's premises.
During the course, they attend classes for a day and then work for five days every week at ALL's shop floor practically experiencing what they have learnt in the classroom. The curriculum has been designed to develop the necessary knowledge and skill base for handling contemporary manufacturing processes such as Lean Manufacturing, TPM, Six Sigma, Supply Chain Management, Kaizen and Kanban. Another external agency, Centre for Excellence in Organisation, has been entrusted with the responsibility of evaluating the progress of the students, which involves putting what they learn in the class room to practical use on the shop floor.
Not only that. The students are paid a stipend by NTTF (out of the grant given by ALL) during this period (70 per cent of prescribed minimum wages in the first year, the minimum wages in the second year and 10 per cent higher than applicable minimum wages in the third and the fourth year).
That apart, NTTF also provides them with medical and accident insurance cover. "Our idea is to enable the students to earn as they learn. ALL, on its part, offers canteen and transport facilities," says Arora. On successfully completing the fouryear course, NTTF awards the students a diploma.
"Currently, 200 students are part of this initiative. We will progressively increase their strength to 1,000 by March 2011," says Alok Kumar Gupta, ALL's plant head at Pantnagar. He is happy with the experiment. "I never thought that 10+2 students will have such a fast learning curve. These people have not even seen an industry before. The first batch has completed over two months on the shop floor. We began commercial production of trucks at this facility on March 25 and have so far rolled out 600 vehicles," adds Gupta.
The man incharge of the class room training, P. Srinivasa Rao, Manager (Training), NTTF, agrees. "They show a lot of enthusiasm and zeal. They come from poor families and have a hunger to learn, come up in life and improve their social status," he says. The students are excelling in cultural construct, too. "We help them develop a new culture when it comes to self management, empowerment, discreet decision making, customer responsiveness and multitasking. They are doing extremely well to understand these concepts. Opportunities for a fast track growth are wide open for them," says S. Denadayalan, Head, Centre for Excellence in Organisation. This is a clear proof that unskilled people in backward areas, when given a chance, can excel, too, adds Arora.
Social Responsibility
While many organisations resort to such training to improve the skills of their employees, ALL's initiative has many unique features. First, the people who are trained are not employees of ALL. They are students of NTTF. Secondly, the students get theoretical and practical training simultaneously and finally, the students— on completion of their diploma—are free to work wherever they want. "We have not entered into any deal with the students. They are free to work for any industry.
We see this more as a corporate social responsibility (CSR) initiative rather than in-house training. Of course, we will give them preference and be more than happy to absorb them if they choose to work in ALL," explains Arora. ALL will take them on the rolls not as shop floor workers, but as executives with equal opportunities for growth.
"They can even become the Managing Director of the company," he adds. Pantnagar facility, in line with the integrated workforce concept, will have no shop floor workers at all! The facility complies with the laws of the land, be it Labour Laws for its employees or the Factories Act.
ALL is spending Rs 12,000 per student. This includes the one-time grant given to NTTF, administrative cost, wastage, loss of volume, cost of classroom and training infrastructure. "We could have got workers at a pay half that money but as I said, this is a CSR initiative for us," chips in Arora. ALL now wants to introduce this programme in its other plants, too.
BLESSING has many advantages. The industry gets factory-ready labour with expertise in modern manufacturing practices. The students graduating from schools and colleges, especially those from below the poverty line, get to overcome a Catch 22 situation— they need to work to gain experience, but they need experience to get work. Moreover, they earn while they learn, thus financially supporting their families. NTTF normally charges Rs 2,800 per month for a similar course. The economy also benefits as poor people from backward regions not only get employed, but move up in terms of status. This leads to a more equitable development.
It also eases migration into cities/towns, which are already collapsing under the weight of massive influx of people in search of jobs. Understandably, the Uttarakhand government is very impressed with the scheme. "This is a great model for bridging disparities and employing rural youth. We are trying to implement it in other industries especially the hotel sector," says Rajesh Naithani, Special Advisor to Chief Minister Ramesh Pokhriyal Nishank and the point person for expanding BLESSING across the state.
But there are challenges, too. Says Arora: "As the programme expands, getting quality students will become difficult. Also, once the students complete their four-year diploma, ALL becomes a fertile poaching ground to tap this highly skilled labour. We need to have the best working environment to retain a good chunk of them. We are working towards it," adds Arora.
ALL'S BLESSING(S)
- Offers the industry 'plug and play' labour with knowledge of modern manufacturing practices.
- Solves a Catch 22 situation.you need a job to gain experience but you need experience to get a job.
- Helps overcome the unemployability-unemployment paradox.
- The students get to earn while they learn. Great for families below the poverty line.
- Enables employment of rural youth and brings about equitable economic development.