Your hazardous waste, my fuel
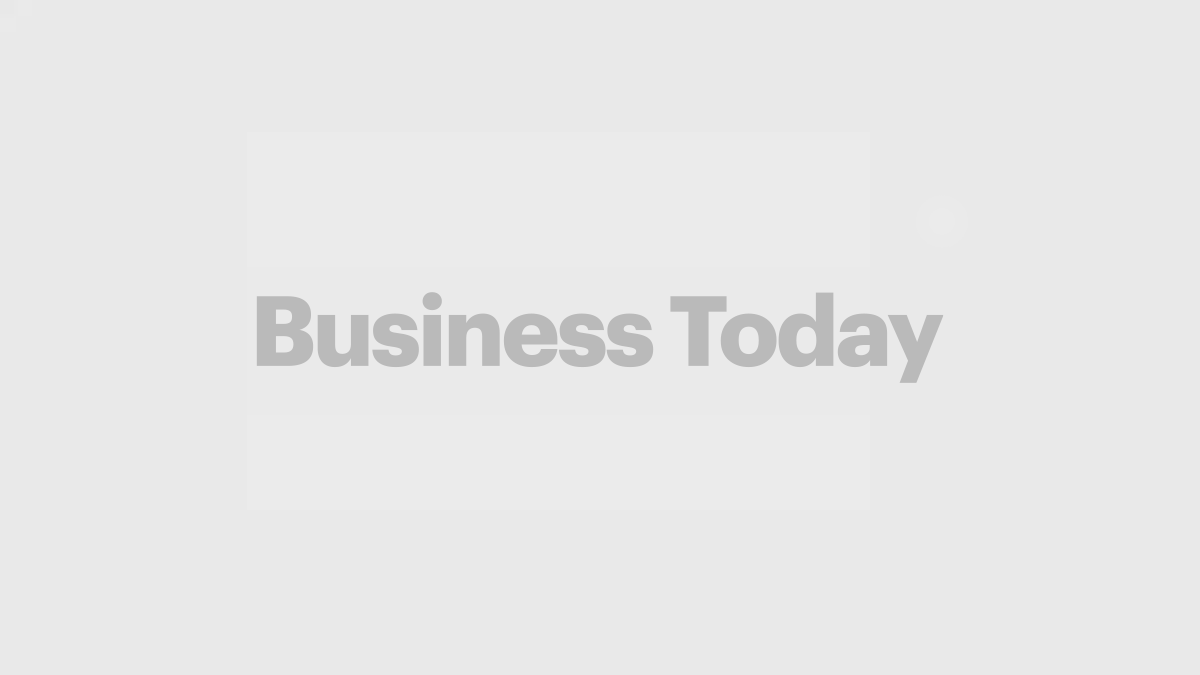
In late 2006 Tom Chackalackal was a worried man. Over 1,000 tonnes of hazardous waste - paint sludge, phosphate sludge, oily rags and other waste from the on-site wastewater treatment plant - had piled up at the factory premises of Ford India near Chennai where it had been producing cars since 1999. As vice president of manufacturing, Chackalackal was hard-pressed to find a way for safe disposal of this humongous waste, which was growing by the day.
The secured landfill that the Tamil Nadu government had promised the company when it agreed to set up a factory in the state had not materialised. Then, Ford India decided to double the capacity of the Chennai plant and foray into the high-volume, small car segment, raising the spectre of more waste.
"It was around this time that Ford's Global Environment team came up with the idea of co-processing. Why don't you burn the waste in a cement kiln like it is done in many countries across the world, they said," recalls Chackalackal. That would have required a partner firm, but nobody was doing such a thing in India then. As luck would have it, Holcim, the world's secondlargest cement maker and a global leader in co-processing technology, had by then established its presence in India with the acquisition of ACC in 2005 and Gujarat Ambuja Cements in early 2006, and was beginning to push its Indian units to co-process.
It had already adopted the technology in 39 countries over the previous two decades. By the end of 2005, it had set up in ACC a new business called Alternative Fuels and Raw Materials (AFR) with the objective of looking for alternative energy sources to fire its kilns. In ACC, Ford India found a willing partner. After getting the necessary clearances from the Tamil Nadu Pollution Control Board (TNPCB), Ford India began shipping its hazardous waste to ACC's Madukkarai plant near Coimbatore for use as fuel in its kiln.
GREEN MANUFACTURING Co-processing... Cuts green house gas emission: Thermal substitution of coal with waste up to 40 per cent in a million-tonne cement plant will reduce CO2 emission by 100,000 tonnes Saves fossil fuel: Considering India's kiln capacity of about 300 million tonnes, even a five per cent substitution will save 2.5 million tonnes of coal annually Disposes hazardous waste safely: It is the most environment-friendly way to dispose hazardous waste as it recovers energy from the waste and leaves no residue Saves money: There is no need to invest in incinerators and landfi lls to dispose the hazardous waste that India generates. India's present cement kiln capacity is good enough for the next decade or more |
Co-processing is the practice of substituting fossil fuel (mostly coal) with hazardous and other wastes in a cement or lime kiln or in a blast furnace of a steel plant. The process is also referred to as thermal substitution and is considered a better way to dispose of hazardous waste compared to a landfill or an incinerator (See Green Manufacturing).
Developed nations have embraced co-processing in cement kilns whole-heartedly. Their rate of thermal substitution is very high. "In developed nations there is a high level of awareness about safeguarding the environment. That is backed by a strong legal framework," explains Ulhas V. Parlikar, Director, Alternative Fuels and Raw Materials Business at ACC. In fact, in 2009, Holcim alone used over seven million tonnes of waste and saved four million tonnes of fossil fuel globally. India is the second-largest producer of cement in the world with an annual installed kiln capacity of over 300 million tonnes. It consumes about 30 million tonnes of coal every year.
Indigenous coal is in short supply. In 2008-09 the shortfall was of the order of 22 per cent and costly imports continue to bridge the gap. In 2009 India generated 67.31 lakh tonnes of hazardous waste. For this quantum of waste the disposal facilities in the country are woefully inadequate.
There are just 25 secured landfills in operation in 12 states and 13 common incinerators in six states. A study by Frost and Sullivan estimates hazardous waste generation in India to grow at a compounded annual growth rate of eight per cent over the next five years. This would call for significant investments in waste disposal facilities. For instance, it costs between Rs 10 crore and Rs 30 crore to put up an incinerator.
In addition, it would cost Rs 400 crore annually to operate the incineration facilities for disposing all the hazardous waste in the country. Given this state of affairs, India should have resorted to coprocessing long ago. But the quantity of waste the country coprocesses now is a meagre 100,000 tonnes.
In 2009 ACC coprocessed 77,751 tonnes of waste substituting 61,965 tonnes of coal. Grasim, Madras Cements and India Cements are some of the other players that have resorted to co-processing but on a smaller scale. Some of the companies that offer their waste for coprocessing are Hindustan Unilever, Cadburys India, Nestle, Johnson & Johnson, Godrej Sara Lee and SRF Nylon.
There are obvious reasons for co-processing not catching up in India. A critical issue here is: Who pays? Globally, the polluter pays. Multinational companies in the country like Ford India follow that practice. But that is not the case with local players. Take the case of fly ash, a hazardous waste generated in thermal power plants. "When the cement industry began producing blended cement using fly ash, it was initially offered free of cost. When demand for fly ash increased, power utilities started charging a price and today it has risen to Rs 400 per tonne," says A.V. Dharmakrishnan, Executive Director, Finance, Madras Cements.
There is a complete disconnect between the user and the giver. Cement firms believe that they are doing the polluting industries a favour by disposing their waste safely. But the industries which give away the waste maintain that they are, in effect, giving the cement plants something that goes to replace fuel and saves money. They see nothing wrong in charging a price for the waste.
"What waste generating industries do not realise is that a cement plant has to invest around Rs 4 crore to create the necessary facilities to process this waste," says P.B. Ravikumar, CEO, GMV Projects & Systems, which specialises in designing and installing alternative fuel handling systems for cement plants in India and abroad.
Resolving this tangle is crucial for the success of co-processing in the country, he adds. The other significant challenge is the legal framework. India continues to accord the same importance to incineration and landfilling as co-processing despite its obvious advantages. There are also no targets for the cement companies for thermal substitution. "There is need for a law with specific focus on co-processing. Today, all we have is a guideline issued by the Central Pollution Control Board (CPCB)," says ACC's Parlikar.
A law, it appears, will have to wait till the CPCB completes its trials. "We are quite positive on co-processing. Trial studies are in progress on all types of waste that can be co-processed. Within one year we will have a clear idea of what to co-process and what not to. Only after this is done can we look at anything more than a guideline," explains Professor S.P. Gautam, Chairman, CPCB. He adds confidently, "Within two years, 100 per cent of all the hazardous waste generated in the country will be co-processed." If one looks at the conditions on the ground, he is quite an optimist indeed.