India's Hydrogen Dreams
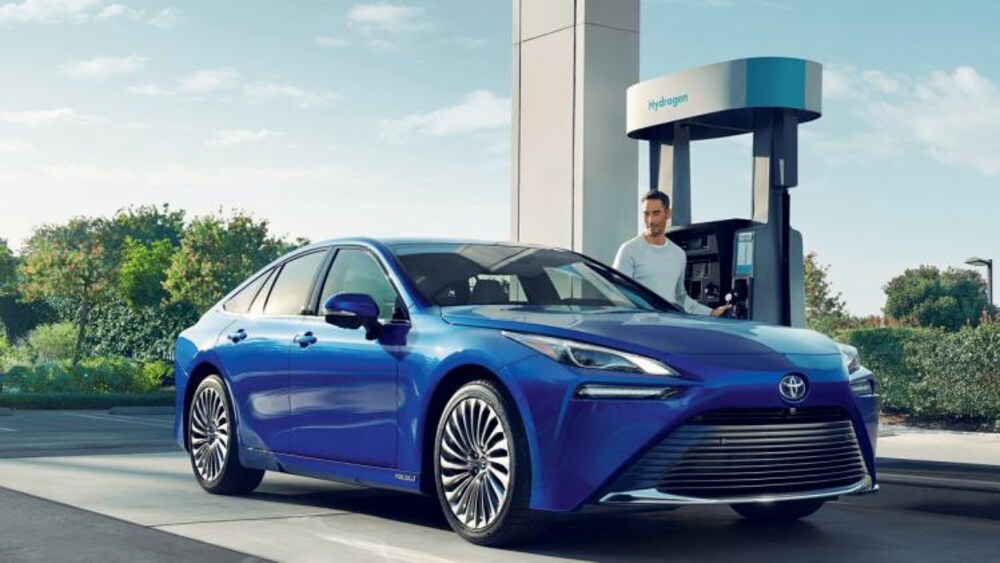
India’s largest company, Reliance Industries Ltd (RIL), made a big splash last week when it announced plans to become a net-zero carbon company by 2035. The Mukesh Ambani-led company is investing Rs 75,000 crore in clean energy projects. A part of it will be used to build an electrolyser and a fuel cell Giga factory, in a big boost to the country’s nascent hydrogen economy. Hydrogen is considered the best way to decarbonise by many industries.
“Green hydrogen will be a unique energy vector that can enable deep decarbonisation of many sectors such as transportation, industry and power. One of the most common methods of generating green hydrogen is by electrolysis of pure water through electrolysers,” Chairman and Managing Director Mukesh Ambani said at RIL’s annual general meeting on June 24. “This brings me to our third initiative — an Electrolyser Giga Factory to manufacture modular electrolysers of highest efficiency and lowest capital cost. These can be used for captive production of green hydrogen for domestic use as well as for global sale,” he added.
It did not come out of nowhere. RIL has been quietly laying the ground for the hydrogen industry of the future. In April this year, the company joined hands with Chart Industries, a Nasdaq-listed global manufacturer of high-end engineering equipment, to form the India H2 Alliance (IH2A). The purpose of the alliance is to work with the government to draw up a blueprint for commercialising hydrogen technologies and systems to build net-zero carbon pathways in India. Since then, JSW Steel has also joined the alliance.
The government has also been keen on hydrogen. Addressing the virtual RE-INVEST summit in November last year, Prime Minister Narendra Modi announced that India would launch a National Hydrogen Energy Mission (NHEM). It found mention in this year’s Union Budget in February when Finance Minister Nirmala Sitharaman set aside Rs 800 crore for the same.
“India has tested the Hydrogen Vehicle. Now we’ve to make ourselves industry ready to utilise hydrogen as a fuel for transport,” Modi said at a webinar after the Budget. “Future Fuel, Green Energy are very important... Hence, ‘Hydrogen Mission’ announced in the Budget is a huge resolution.”
This wasn’t the first time the government has talked about hydrogen. In fact, India had a head start when in 2006 the first Hydrogen and Fuel Cell roadmap was announced. But progress has been tardy since then even as others have marched ahead. Europe and the US have taken the lead in electrolysers and fuel cell electric vehicle (FCEV) technologies; Japan and Korea are investing heavily to become global champions of hydrogen usage, while Australia and Chile are building global green hydrogen production hubs.
The potential for hydrogen to reduce carbon emissions in India is immense. The demand for hydrogen is around six million tonnes (MT) per annum, with most of the consumption coming from fertiliser plants and refineries, according to TERI. It needs to go up to 28 MT by 2050 and 40 MT by 2060 if the net-zero carbon target is to be achieved. The demand will be steeper if the deadline is shortened. Potentially, hydrogen can also save over $160 billion worth of imports for India — $112 billion on crude, $9.6 billion on natural gas/LNG, $23.6 billion on coal, $16.2 billion on petroleum products and $775 million on ammonia.
Decarbonising Industries
One of the biggest impacts of clean energy sourced from hydrogen will be on the industrial side where it can be used to decarbonise a host of sectors such as power, steel and oil refineries, cement factories, ports and logistics. Primary steel production needs chemical feedstocks like direct reduction of iron ore, which direct electrification does not provide.
“There have been multiple studies done globally as well as in India, on the potential of hydrogen to drive decarbonisation in sectors such as steel, chemicals, fertilisers and heavy duty transport/freight,” says Jill Evanko, CEO and President, Chart Industries. “Steel and cement seem most attractive from a short-to-medium-term perspective followed by fertilisers and chemicals on the industrial use case side. In the long term, this could extend to mining,” he adds.
Sajjan Jindal’s JSW Group wants to be one of the early adopters and considers hydrogen to be at the centre of its plan to go carbon neutral in future. “There are a number of green steel initiatives currently underway but use of green hydrogen in the steel-making process is one that would make the most significant decarbonising impact going forward,” says Prabodha Acharya, Chief Sustainability Officer at JSW Group. “We are uniquely placed to lead on the green hydrogen topic as we have a portfolio of businesses with significant interests in steel, cement and renewable energy. Working with a multi-sectoral approach and across the hydrogen value chain is the right way to build the hydrogen economy in India.”
But there are challenges, the biggest of them being the cost factor. While hydrogen is one of the most abundant elements, it cannot be sourced as gas from the atmosphere since it is lighter than air. Instead, it has to be separated from other compounds like water.
Two of the most common ways to do that are steam forming and electrolysis or water splitting. While steam forming is less expensive, building plants for scale is still a costly proposition. Also, this process produces greenhouse gas emissions that defeat the main purpose of opting for hydrogen in the first place.
The other method of electrolysis involves passing electricity through water to separate it into basic elements, hydrogen and oxygen. It is a very expensive process, and the IH2A is looking to devise a strategy to make it economical.
The alliance has made a six-point submission to the government that talks about among other things, an aim to create a national electrolyser installed capacity of 15-20 gigawatt (GW) and a national hydrogen-themed energy transition fund with a target of raising $ 1 billion by 2030 for deployment of projects of a certain scale. It also calls for setting up a public-private task force, globally harmonised and interoperable hydrogen standards, pre-feasibility studies of at least 10 hydrogen hubs and an industrial group that can look into specifics of using hydrogen as a decarbonisation tool.
“As the global use for hydrogen develops, economies that develop local supply chains for hydrogen systems — whether for electrolysers, storage equipment or sub-stack systems for fuel cells — will be the ones to benefit from the economies of scale,” says Evanko of Chart Industries. “The availability of public and private funding for hydrogen projects will be another key determinant of national success on hydrogen commercialisation.”
Hydrogen can help India in geopolitics too. In electrification, India is behind the curve as far as securing key raw materials such as lithium and cobalt is concerned. China has a head start there and experts are worried India may end up being dependent on others for lithium in the same way it is for crude oil right now. In hydrogen, on the other hand, the industry is still nascent with no country having a definitive edge. It offers a much-better chance for India to nudge ahead. Ambani’s big play aims to tap into this opportunity.
Green Transport
Another area where hydrogen can play a significant role is transport. India has embarked on an ambitious plan to electrify its two- and three-wheelers and passenger vehicle segments. Doing the same for long-haul freight trucks, however, poses a problem since lithium-ion batteries do not have the range for intercity trips. They also need longer time to charge, which could potentially keep the trucks off road.
Hydrogen can solve both the problems. In an FCEV, electricity needed to run the vehicle is produced in the fuel cell stack where hydrogen is fed through the tank. This can be refilled in a matter of 5-15 minutes, compared to recharging a battery EV truck that could take hours.
“We believe EVs and FCEVs will co-exist with EVs being preferred for short runs in cities, while FCEVs will be used for long-haul transportation,” says Vikram Gulati, Country Head and Senior Vice president, Toyota Kirloskar Motor.
Like in the case of industrial use, cost is a hindrance here as well. Currently there are only three brands that offer hydrogen-powered fuel cell vehicles worldwide — Toyota Mirai, Honda Clarity and Hyundai Nexo. The Mirai is priced upwards of $50,000 or Rs 37 lakh, which would make it out of reach for most Indians. This is also much more expensive than EV offerings such as the Hyundai Kona at Rs 24 lakh or MG ZS EV at Rs 21 lakh. If imported, the price of an FCEV would double, expanding the gap with a comparable EV or petrol/diesel product even more.
“Eventually, hydrogen is expected to play a major role in the global energy mix, but is still in its infancy and requires a lot of investment before it becomes commercially viable,” say Amit Kapur, Joint Managing Partner and Akshat Jain, Partner, J. Sagar Associates.
No wonder then, carmakers are yet to warm up to the idea of fuel cell vehicles (FCVs) in India. It is a different story in commercial vehicles, where an FCEV has a significantly better chance of success, compared to a pure-play battery EV truck or bus. Commercial vehicle makers are already working on this. India’s largest CV maker Tata Motors has showcased FCEV buses at different auto expos. Recently, it also won a tender for supply of 15 FCEV buses to Indian Oil Corp. To be used in Delhi/NCR, these buses are part of a first-of-its-kind joint project to take the hydrogen and fuel cell journey in India to the next level.
“Key benefits that hydrogen has over lithium-powered battery electric vehicles are — high-energy density, faster fueling time, long-range applications which become non-viable with BEV (battery electric vehicle) due to LI-Ion battery constraints (weight, size and cost for high capacity batteries),” says Rajendra Petkar, President and CTO, Tata Motors. “On a standalone basis, hydrogen fuel cells for EVs are more eco-friendly as they do not have emissions related to metal oxide processing and recycling. Lithium-ion batteries also have concerns about continued long-term supplies of rare earth materials and severe supply chain constraints. From an application standpoint, fuel cells make sense for trucks and buses, and high-end SUVs.”
Even in commercial vehicles right now, an FCEV costs significantly more than electric or diesel-powered trucks and buses. But the gap is expected to narrow in the next five years. India still does not have an FCEV truck or bus available in the market for a cost comparison, but in Europe, the total cost of ownership (TCO) of an electric truck is still lower by 20 per cent, compared to an FCEV truck. In case of a fossil fuel-powered vehicle, TCO is 35 per cent lower, compared to an FCEV. The biggest reason is the disparity in the purchase price of the vehicle. But FCEV costs are expected to fall, and together with policies that penalise fossil fuel vehicles, the TCO of an FCEV in countries, including the UK, Latvia, Estonia and the Netherlands, is expected to fall below fossil fuel vehicles by 2024. It is a trend likely to be replicated in India, too, albeit with a few years lag.
Hydrogen contains more energy — 130 megajoules per kg — compared to petrol or diesel (45-46 MJ per kg), which means it offers better range on a full tank. A car consumes 1 litre of hydrogen to cover around 28 kilometres, compared to around 18 kilometres for a litre of petrol. But, the current price of hydrogen in India is estimated at Rs 880 per kg, which increases the fuel cost. Lack of hydrogen-dispensing stations is another roadblock.
“The future of FCEVs depends on its performance and cost-competitiveness. FCEVs have a higher TCO mainly due to the initial acquisition cost, driven by input prices of fuel cell stack, balance of power plant parts, hydrogen storage and EV propulsion system-related parts,” says Tata Motors’ Petkar. “As these cost go down, with government incentives and localisation of parts, the overall economics of FCEVs is likely to improve. Market demand and increased volumes are expected to occur during the second half of the current decade.”
According to Niti Aayog, low cost of renewables that powers the grid together with economies of scale in future can lower the cost of hydrogen fuel to $4 per kg. At that level, an FCEV truck will become competitive with its diesel counterpart.
“The price of delivered power is the biggest driver of cost for green hydrogen. The recent bids of around Rs 2 per unit for solar power in India are among the lowest in the world. We also have competitive wind tariff, which gives us the advantage to disrupt the hydrogen industry,” says Amitabh Kant, CEO, Niti Aayog. “If we make the right policy decisions, we can be a net exporter of hydrogen by 2030 with a cost of just $1.5 per kg. Manufacturing electrolysers is a huge $20-billion opportunity.”
The higher energy content of hydrogen poses risks as well. Automotive fuels are highly inflammable, but a vehicle laden with hydrogen is likely to be more vulnerable in case of a major accident. Hydrogen-dispensing stations would need to adopt to more stringent safety measures.
Having missed out on many technology-led innovations in the past, hydrogen presents India with the opportunity to lead the change. The parts of the puzzle just need to be put together.
@sumantbanerji