The FAB Challenge
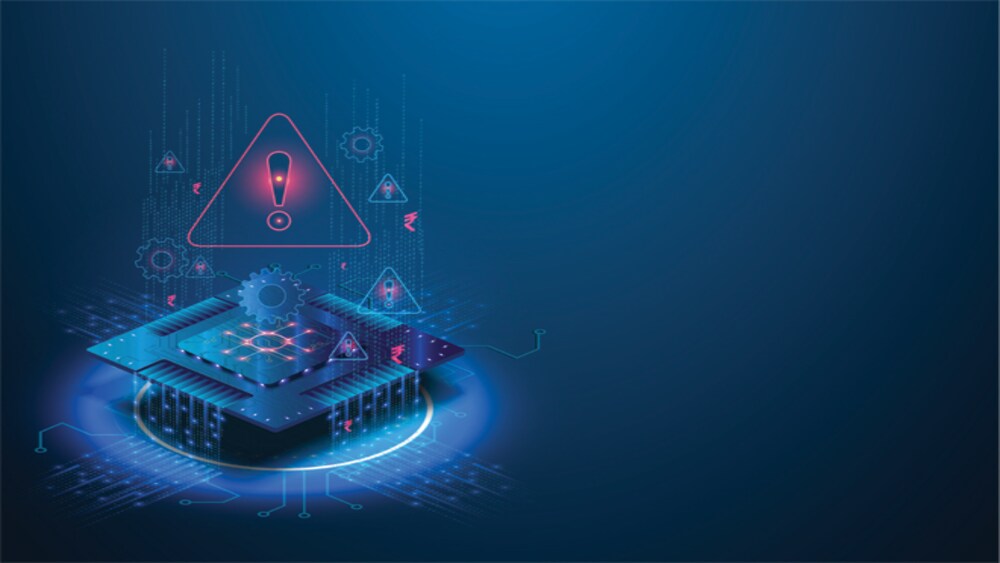
India's largest automotive component maker Bosch faced an unforeseen situation in early December - shortage of semiconductor components. The reason was surge in demand for consumer electronics globally due to work from home and rise in adoption of 5G in household appliances.
This could not have come at a more inappropriate time. Demand for automobiles was just beginning to rebound after a torrid first half of the year when production was disrupted due to lockdown in April-May. Another disruption can impair the recovery, which is what Bosch warned in a letter to market regulator Sebi. "Imports of Bosch Ltd have been impacted with severe shortage of imported micro-processors (semiconductors), leading to reduced ability to deliver to the automotive market demand in India," it said.
Disruption in supply of even a single part in the $120 billion automotive industry can bring the entire sector to a standstill. Two days later, utility vehicle major Mahindra & Mahindra said it was bracing itself for after-effects of the disruption at Bosch. "Operations of the company in the automotive sector will be affected by global supply shortage of micro-processors (semiconductors) used in electronic control units (ECUs) which are supplied by Bosch," it said. "It is not clear as to what extent and for how long the shortage of semiconductors will impact vehicle production in India. Any stoppage of vehicle lines has a resonating effect on the entire auto component manufacturing ecosystem," says D.K. Jain, President of the Automotive Component Manufacturers Association (ACMA).
Microprocessor chips, the brain behind computing in modern electronic appliances, are produced in high technology facilities called semiconductor fabrication units or simply FAB units. A shortage affects the entire consumer electronics segment and not just the automobile industry. Operations at Lava and Micromax that are trying to make a comeback in the domestic smartphone market have almost stuttered to a halt due to shortage of chipset supplies from Taiwanese firm MediaTek.
The examples brutally expose the soft underbelly of India's electronics industry - its heavy reliance on imported components. The industry imported components worth $50 billion in 2019. Aware of the dangers of such high import dependence, the government has rolled out ambitious production-linked incentive schemes to encourage production of a host of these components in the country. The most important here is chips, the central component of any electronics item. India has negligible semiconductor manufacturing. As the industry expands - the market is poised to double to over $500 billion by 2025 as smart devices become intrinsic to a host of other sectors (autonomous or electric cars for example) - the demand for chips will rise manifold. "The electronic content in vehicles has been progressively rising and incidents such as these only make obvious the need for localisation and self-reliance in auto electronics," says Jain.
As the current disruptions show, it is an area where India can ill-afford to depend on others. It was not a coincidence then that on December 15, the government invited fresh proposals from the industry for setting up FAB units in the country. It is the start of a long journey. India's past failures in the area show the going will not be easy.
Attempts Galore
This is not the first time India is trying to build FAB units. The first attempt was made back in 2006 when Bangalore-based SemIndia signed an MoU with the Andhra Pradesh government to set up a wafer manufacturing SEZ for which it was allocated 1,200 acres. The $3 billion project could not take off. The state government suffered a loss of Rs 300 crore.
Around the same time, the government tried to woo global tech giant Intel to set up a semiconductor facility in India. Instead, Intel went to China. In 2011, the government came up with its maiden National Electronics Policy and invited proposals for setting up FAB units. It received more than two dozen expressions of interest. Two were given the nod in 2014. Both could not take off due to a number of reasons, including inability to tie up funding and unviable business case. The two biggest roadblocks were the high investment required and demand uncertainty. "Semiconductor manufacturing requires huge investments, natural resources and highly skilled manpower. In India, we are deficient in all these due to which no significant semiconductor manufacturing is happening," says Sanjeev Agarwal, Chief Manufacturing Officer at Lava Mobiles. "The government will have to come up with policies which can overcome these deficiencies. This may require co-investment in the beginning. Local manufacturing of semiconductors like processor, memory, etc., which are major constituents of mobile phones and other electronic products, will play a major role in making us atmanirbhar."
Making semiconductors involves front-end fab manufacturing and back-end assembly. While India has developed considerable expertise in the back end - packaging and testing - there are only a handful of companies globally that produce chips on a large scale. None of them are in India. As a result, almost all chips, units and displays have to be imported. Estimates suggest that value of chip imports alone could be more than $12 billion in FY21.
"Setting up a FAB unit is not easy. Investments required for an advanced FAB factory might cross billions of dollars," says Sanjay Gupta, Vice President and India Country Manager, NXP Semiconductors. "Any company would like to know likely returns, how long it will take to build the plant and then how soon it will start getting returns. Even if you give 100 per cent subsidy, if there is no buyer, you will not be able to earn any returns. A single day operation costs millions of dollars," he adds.
That is why, in countries where chip manufacturing has taken off, be it China, Taiwan or South Korea, governments have been generous in putting the initial capital. This is apart from incentives like low interest rates and tax holidays. India will have to do more of the same as only a few companies in India have the required balance sheet strength. "The government has to offer significant incentives. For example, if it takes $100 to put up a FAB unit and the government puts in $40, the investor still has to get $60. The investment community has to feel confident that they are going to get returns. We have not been able to crack that part of the story," says Satya Gupta, Chairman, India Electronics and Semiconductor Association (IESA). "The government can work with one of the large business houses in India, let's say Reliance or Tata. They don't have to necessarily put up the entire 60 per cent money but can lead with 10-15 per cent to create a consortium with international partners. We have not tried this in the past. It's worth a shot." To be fair to the government, it did offer capital subsidy of 20-25 per cent of the project cost in previous instances too, but with rigid minimum investment thresholds.
The problem of demand aggregation is also unsolved. The investments are not one-off. As technologies evolve, the factories have be updated, which means big investments every four-five years, if not less. The short time span for earning returns makes it a tricky business. "Every company will have to take a look at its own supply and demand. Incentives by governments make decision-making a bit easier but it's not just about that," says Anand Ramamoorthy, Managing Director, Micron Technology India. Micron is the world's fourth-largest semiconductor company. "A lot of other things have to fall in line for front-end manufacturing to take place. To be honest, not more than eight or nine countries have successfully established wafer-level manufacturing."
An estimated 75 per cent of global semiconductor capacity is concentrated in East Asia. According to a US Semiconductor Industry Association and BCG report, Taiwan is the leader in FAB capacity with 22 per cent share in 2020, followed by South Korea (21 per cent), Japan (15 per cent), China (15 per cent), the US (12 per cent) and Europe (9 per cent). It also said that majority of new capacity in the world, 40 per cent, is being added by China, which will make it the leader in the space by the end of this decade. The largest dedicated semiconductor foundry company in the world is Taiwan Semiconductor Manufacturing Company, followed by Intel Corp, Samsung, Qualcomm, Broadcomm Inc and Micron Technology Inc.
Policy Framework, Supplier Ecosystem
Capital may be the first obvious stumbling block but is not the only one. Like any big factory, a chip unit needs a battery of ancillary units nearby for supplying parts or for maintenance and upkeep. These are as high-tech and capital intensive as the main unit. Take specialised cryo technology-based pumps, which are not produced in India at all. "These are very high-technology pumps and we don't make them here," says Srinivas Satya, Managing Director, Applied Materials India, which supplies equipment, software and services to chip-making firms. adding that "there is a huge secondary industry around FAB units, companies that service, clean, refurbish or provide other critical services to these factories. Unless they are here, no big player will invest in the main manufacturing unit."
The other worry is whether India has the appetite for something as long term as this. There may not be an overnight fix for other requirements such as top-class connectivity, low logistics costs, skilled manpower, superior power infrastructure and abundance of pure water. However, the government can guarantee a stable policy regime.
"One of the inputs we have got from global players is that it has to be a long-term engagement. Announcing a policy for three-five years does not work," says Gupta of IESA. "You need to give a kind of assurance to the investor that for at least 15 years, policies, incentives and all of those things will remain even if governments change."
Unlike other manufacturing industries where localisation starts from smaller uncomplicated nuts and bolts, in electronics, the chip is itself a seemingly small yet highly sophisticated part. Mastering this is often the big last in a series of smaller steps. The government has taken one of these smaller steps with production-linked incentive scheme for mobile phones, which has got off to a good start. Thanks to the scheme, which gives manufacturers an incentive of 4-6 per cent on incremental sales, and the broader phased manufacturing programme, the number of mobile phone factories in India has gone up from just two in 2014 to over 250. The government has announced plans to roll out similar schemes for other electronic components too. "We have initiated talks with the industry to prepare a blueprint on getting FAB units in the country. We are attaching top priority to this," says a senior official in the Ministry of Electronics and Information and Technology. "It may not be easy and there are many challenges but we are determined. We are also studying why it did not work in previous instances. We hope to soon put in place an effective and attractive policy."
The China Angle
There is a profound China angle to this. More than half of India's electronic imports, $50.7 billion in 2019, are from China and Hong Kong (29.1 billion). Silicon chips are a significant contributor. In fact, around 20 per cent of India's electronics imports are microprocessor chips, with China having a disproportionately large share of 70 per cent (accounting for $7 billion of India's $10 billion chip import bill). India needs to manufacture its own semiconductors to reduce the leverage China has, something that has been clearly highlighted in a report by the India Cellular and Electronics Association (ICEA).
To begin with, ICEA has pitched for incentives similar to the PLI Scheme for printed circuit board assembly, the green colour board inside electronic gadgets that mechanically supports and electrically connects the components. The current market size for PCBAs in India is $16 billion (FY20), expected to grow to $87 billion by 2025-26, representing a $71 billion opportunity in the domestic market alone. Thanks to the PLI Scheme for mobiles and smartphones, ICEA expects 90-99 per cent of PCBAs to be locally assembled in future. Smartphones comprise over 80 per cent of the PCBA market.
"As more electronics capacity is set up in India, that may, in turn, bring in more vendors and players. Over a period of about five years, India might be able to boast of a credible electronics manufacturing ecosystem," says the ICEA report. "If the scale becomes sufficiently large, it could trigger designing and manufacturing of multilayer PCBs in India. Production of semiconductor chips Assembly, Testing, Marking and Packaging ('ATMP') could also become a reality. This is how it had panned out in China."
"Should PCBA operations start on a global scale in India, semiconductor chips can be imported by India directly from Korea, Singapore, USA, Japan and Germany, and there may be no need to import from China," the report adds. "It will help us achieve the strategic objective of reducing dependence on China." Achieving some scale in PCBA production will help in manufacturing of more capital intensive and complex parts. It is a model that has successfully worked in China. "We have just about started the journey of becoming self-sufficient in electronics. There is quite some distance we have to cover," says Pankaj Mohindroo, Chairman, ICEA. "We have to take many intermediary steps. Production of PCBAs is one such step. Once we start to do that, the ecosystem for chip manufacturing will be created."
The odds for now are stacked against FAB units in India. However, India cannot afford to not be in the game.
"In case there is a global crisis or political isolation, India has to be self-reliant. If tomorrow countries manufacturing chips decline to supply to India, our whole ESDM (electronic system design and manufacturing) can come to a standstill," says Gupta of NXP Semiconductors. "If our own chip factories are there, let's say even a decade from now, that will be a big strategic advantage. Otherwise we will always be dependent on other countries."
The invisible yet omnipresent chip will thoroughly test India's resolve of becoming truly atmanirbhar.
@sumantbanerji