Golden harvest
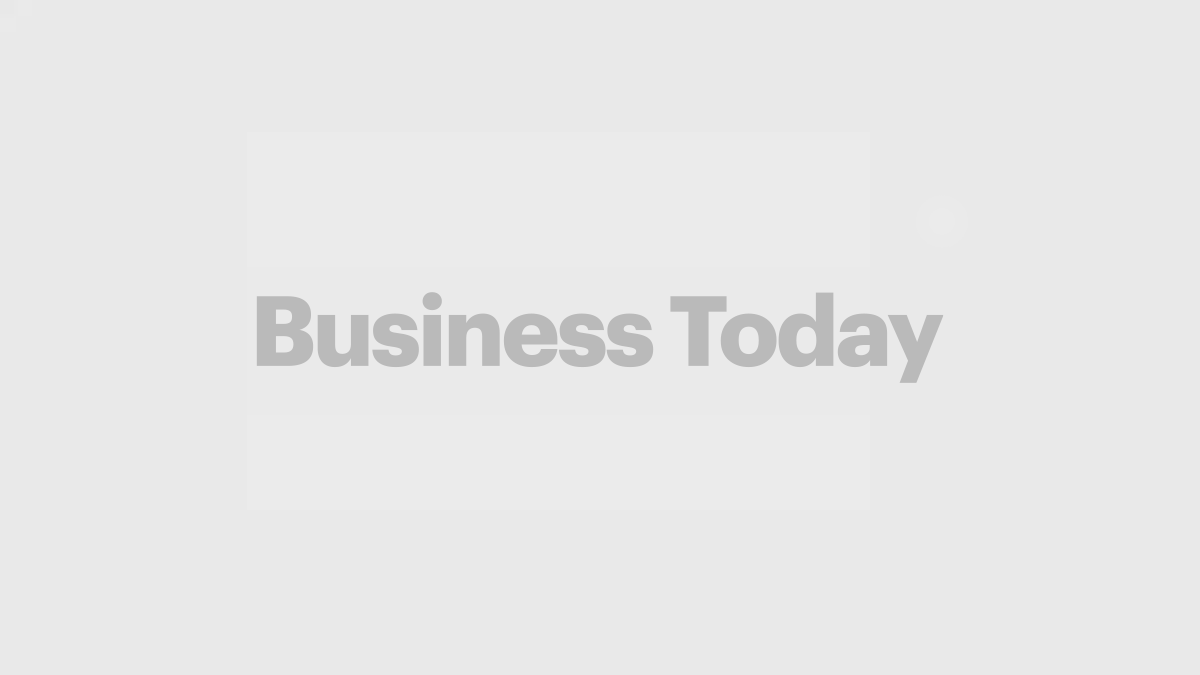
Crude oil.... It permeates our life so comprehensively! Diesel, petrol, LPG, plastics, paints, chemicals, pesticides, pharmaceuticals, non-cotton clothings…all these and much else are derived from it. So, when I recently got the opportunity to visit India’s newest and largest onshore source of crude, Cairn India Ltd. oilfields in Rajasthan’s Barmer district, I was curious and excited.
That the sands of Rajasthan underlay a potential goldmine of petroleum reserves has been debated for a long time. The inauguration of the Cairn oilfield by the Prime Minister on August 29 settled that debate. Never mind that it took two attempts to nail the reserves. Anglo-Dutch giant Shell had explored the same region in the late 1990s and concluded that it contained no major oil reserves. Cairn India, the local arm of UK-based Cairn Energy Plc., took over in 2002 and just two years later struck a reserve that is expected to account for 20 per cent of India’s oil output in 2011!
6,80,000: India’s current daily oil output in barrels |
1,75,000: Daily output in barrels from Cairn’s Rajasthan wells by 2011 |
$124 billion: India’s yearly oil import bill |
Rs 20,000 cr: India’s annual savings on oil import due to Cairn oil |
20% will be Cairn’s contribution to India’s oil output |
But, as I was to realise during my day’s trip, more fascinating than the tale of discovery is the process of taking out the crude from the earth. From the use of sound waves to distinguish between water and oil and melting the crude-laden wax by injecting hot water to building a 700-km pipeline that has to be kept at a temperature of 650C throughout—all this and more is needed to turn the crude into things useful. But all this was far away from my mind when we touched down at the Utterlai airbase near Barmer city and headed for the Mangala Processing Terminal (MPT), 20 km away in a bus. We cut across a desolate, sandy landscape, the monotony of which was finally broken when the towering structures of MPT began to materialise on the horizon.
At the MPT, a crowd of a few thousand people has gathered to witness the inauguration of first oil by Prime Minister Manmohan Singh. The land we are standing on is part of the 3,111 sq. km of oil blocks—Mangala, Bhagyam, Aishwariya, Saraswati and Shakti. The inauguration is an elaborate affair marked by a corporate presentation by Cairn and speeches by the CM and the Union Oil Minister. “Initially, the Mangala field, the largest of 25 oil and gas discoveries made in Rajasthan, will produce 30,000 barrels of oil per day (bpd) and reach a capacity of 50,000 bpd by the end of 2009. This will be supplemented by 40,000 bpd from Bhagyam and 10,000 bpd from Aishwariya fields to reach an overall plateau production of 1,75,000 bpd by 2011,” says Rahul Dhir, MD and CEO, Cairn India, in his welcome note.
Sound of oil
The ceremony and the lunch over, the BT photographer and I along with a few Cairn officials hop into a Toyota Innova for a tour of the MPT, which is spread over 400 acres (roughly the size of 200 football fields) and crisscrossed by 80 km of roads. As we head towards the Processing Trains, the nerve centre of the oilfield, we are informed about the exploration process, which begins with seismic data acquisition. It involves sending sound waves into the earth’s surface and measuring their amplitude when they bounce back. The amplitude differs for each of the substrates like water, soil, crude oil, etc. The actual availability of hydrocarbons in an area is assessed by testing the underground rock samples in a lab. Full-fledged drilling is undertaken after an economic development plan is prepared.
We pause briefly at a 100 ft. high mobile drilling rig. Cairn is using a horizontal drilling technique, which allows 20 wells to be operated from a single drilling pad. “This is being done as part of our zero local dislocation policy and efforts to minimise our footprint…and will reduce our surface footprint area by over 90 per cent,” says Santosh Chandra, Director (Trading Operations), Cairn India. So far, 36 oil wells have been drilled but just two are operating. By 2011, Mangala alone will have around 100 wells. During the life of the project, i.e., 40 years, the company plans to dig at least 300 oil wells in the entire Barmer basin. Here, Cairn has to dig as much as 1,600-1,800 metres below the surface to reach the crude oil.
Waxing out crude
Another thing about the Rajasthan deposits is its high wax content, which makes it difficult to suck out the crude. “This is dealt with by heating saline water and pumping it into the oilfield, which flushes out the waxy crude,” says an official, adding that for every barrel (1 barrel=160 litres) of oil, 1.1 barrel of water needs to be injected into these wells. Cairn transports this water through a pipeline from Thumbli, a saline water reservoir 22 km from MPT. Later, Cairn plans to add polymers to the water before injecting it. This will increase the recoverable reserves from the oilfields. “Of the total estimated oil reserves of two billion barrels, an enhanced oil recovery (EOR) mechanism will help us extract almost one billion barrel of crude oil,” says D.K. Venkatesan, Head (Projects), CIL.
65 degree Celsius pipeline
Finally, we arrive at Train One, a complex maze of pipelines, through which raw crude consisting of oil, gas, dust particles and water gets processed as it passes a slug clutcher, production fluid heater, production separator settling tank and dehydrator. The water, after it is separated from the crude, is treated and injected back into the wells. Train One has a capacity of 30,000 barrels of oil per day (bpd). MPT will have three more trains, with the last one scheduled for commissioning by 2011.
The processed crude from Train One collects into two export oil storage tanks—each the size of five and a half swimming pools—before being loaded into tankers that will carry it to Kandla in Gujarat, from where it will be shipped to MRPL’s refinery in Mangalore. By the year-end, crude will be shipped from MPT via a 700-km heated pipeline—the world’s longest such pipeline—that Cairn is building from Barmer to Bhogat on the Gujarat coast at a cost of nearly $1 billion. This pipeline will cover two more delivery points: Viramgam and Radhanpur terminals, which are connected by pipelines to IOC’s Koyali, Panipat and Mathura refineries. “Thirty-two gas-powered heating stations are being set up along the pipeline at a distance of 18-20 km from each other to keep the temperature in the pipeline at 650C for smooth passage of crude,” says Chandra.
Quality and cost
As we leave Train One, we remember to ask about the quality and economics of the Rajasthan crude. We are told it has an API (American Petroleum Institute) specific gravity of 27.41, which makes it medium-grade crude with low sulphur content, like the Duri crude of Indonesia but inferior to Brent—a benchmark grade for crude. Initially, Cairn plans to sell at 10-15 per cent discount to Brent. The total cost to Cairn per barrel works out to $10—exploration and development $3.5, operating costs $5 and pipeline $1.5.
It’s late afternoon by the time we prepare to leave the MPT. I look around me and the desolation and barrenness of the surrounding landscape suddenly seems comforting.