Leveraging Global Supply Chains
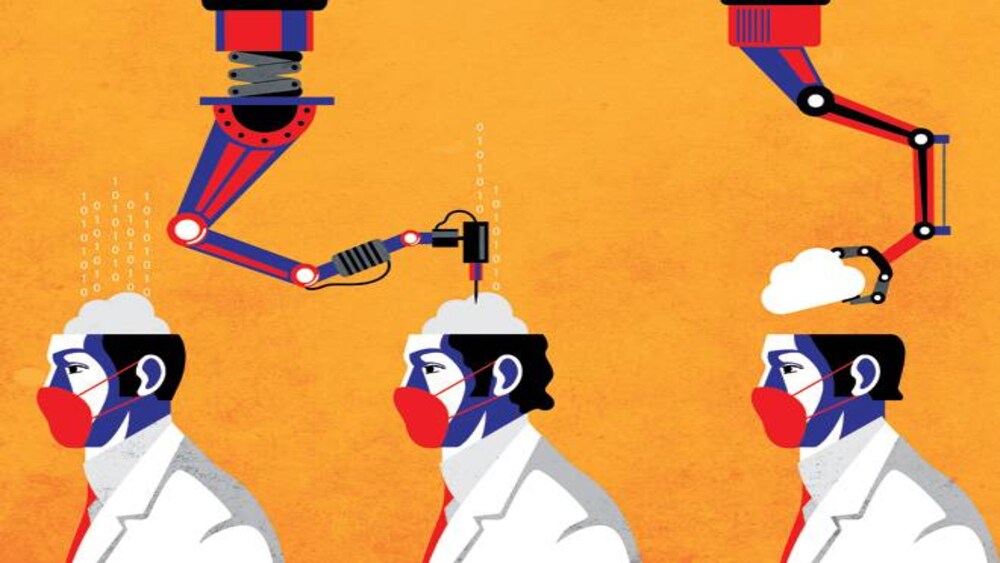
Every crisis brings an opportunity. The recent disruptions to the global supply chain have accelerated the shift towards shorter development times, shorter product life cycles and frequent adjustments to customer demands. And the entire value chain is reacting to these changes.
The challenges on labour, sourcing, distribution and delivery logistics have made companies rethink ways to keep supply chains globally competitive, with regard to safety, quality, delivery, cash and cost. As manufacturers put a premium on health and safety of their people, they also have to make short-term and long-term decisions to ensure business continuity.
India is uniquely positioned to benefit from this transition.
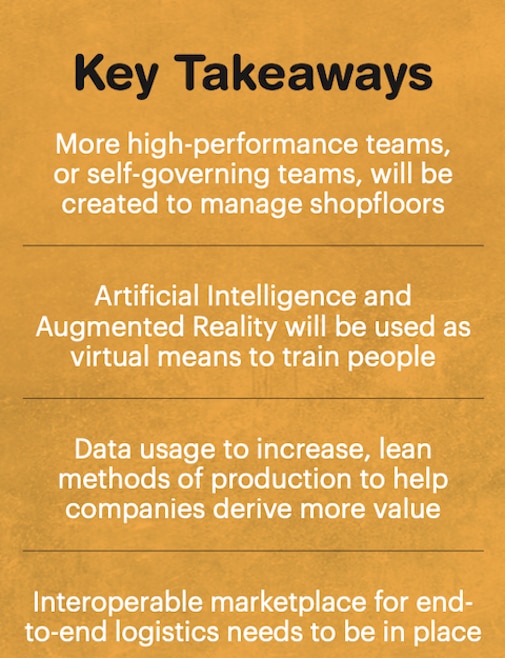
Capital goods manufacturing in India is around $40-50 billion. There is potential to double that amount in the next 5-10 years. India imports capital goods worth $40-45 billion which presents a huge import substitution opportunity. With 25 per cent share of global science and engineering graduates, India's engineering and R&D talent is sought globally.
If the right policy reforms, infrastructure and logistics support is provided, India has every reason to take advantage of the current wave of advanced manufacturing. This is indeed the time to think big and leverage the support being provided by the Indian government under Aatma Nirbhar Bharat and other initiatives.
Data intelligence-driven manufacturing
Technologies such as Internet of Things (IoT), Cloud computing, 5G, Artificial Intelligence, Additive Manufacturing, Digital Twin, Blockchain and Robotics are impacting almost every aspect of manufacturing. The true value from implementation of these advanced technologies can only be derived when enormous volumes of data is translated into insights, which can then be applied to optimise operations, including reducing downtime and manufacturing costs.
Using predictive algorithms, Big Data management and Analytics engines, the factories of the future will be able to marry the digital and the physical world. The concept of Digital Twin is increasingly finding use cases in manufacturing.
The role of R&D centres in developing and implementing advanced manufacturing techniques cannot be overstated. India's rank on the Global Innovation Index improved from 81 in 2014 to 52 in 2019. Can India move to top 20 in the next five years? Of course we can, provided we continue on this path by attracting higher investments in research & development (R&D) in the private sector, including those to support advanced manufacturing.
These technology interventions have to go hand-in-hand with reskilling human resources and strategic workforce planning. It is important to bear in mind that a learning culture is key to competitiveness.
Data by itself is no good if it doesn't get translated into timely smarter decisions. One has to retrain the workforce to embrace technology, innovation and democratise data.
To make all this work together, human capital is a critical asset. The creation of High-Performance Teams or self-governing teams is crucial where empowerment, ownership and data is provided to each person for driving customer outcomes and value through a process of continuous improvements and learning at the shop-floor.
Artificial Intelligence (AI) and Augmented Reality (AR) are useful as virtual means of training and skill development. They enable shorter learning curves for the machine operators and robust processes due to quicker feedback to product and process development teams. Remote monitoring of the processes through AR and IoT hardware enables simultaneous launches of products in different markets.
Driving convergence of digital, lean and sustainability
Manufacturers globally are continuously striving to make their operations more efficient, more productive, which can show up to stakeholders in various ways, including an improved bottomline. Manufacturing, powered by data and streamlined by lean methods of production, allows enterprises to derive even more value, including accelerating their competitiveness, greater productivity, uncovering root causes of wastage before they become problems as well as lower costs. All of these matter to stakeholders.
Development of new materials and processes has a significant role to play in allowing use of recycled and recyclable material, thereby reducing environmental impact, disposal cost and reduction of waste. One of GE's group companies that has done significant work in the areas of material development as well as implementing lean practices and has seen extraordinary results is LM Wind Power, a leading global manufacturer of wind blades. The agility in adapting lean practices on an ongoing basis is key to empowering the machine operators to do continuous improvement to derive greater value and enhance flow. Lean best practices are very effective in simplification and subsequent digitisation of processes.
Another key aspect to take into account is sustainability and carbon footprint. In this area, LM Wind Power - a carbon neutral business since 2018 - is known for its experience and investment in blade design and manufacturing, while at the same time considering environmental impacts throughout the product life cycle. A wind turbine blade creates clean energy for more than 20 years. However, manufacturing, assembling and transporting the blades requires resources and energy and produces waste. LM Wind Power works to reduce environmental impact in all aspects of a blades life cycle - continuously introducing efficiencies and innovative solutions in the blade manufacturing processes to reduce emissions, while also conceiving materials with a view of being able to enter into a circular economy.
Maintaining globally competitive supply chain
Supply chains can be a make or break opportunity. Leading manufacturers have highly sophisticated supply chains, critical to their competitiveness. Recent developments have been threatening global supply chains of almost all manufacturers. This has led companies to evaluate their traditional supply chain for a more flexible and even digital network. Flexible sourcing and digitisation will be important for manufacturers to building a smarter supply chain - one that stands the test of disruptions. By improving their ability to receive real-time information and analyse internal and external data, business leaders can act based on early indications of possible supply chain disruptions.
To fully understand and manage their operations, manufacturers must be able to visualise, analyse and optimise every aspect of their processes, equipment and resources. When all of these aspects come together, companies can boost production line uptime and asset performance, as well as the safety and reliability of valuable equipment. An efficient global supply chain must be enabled by seamless digital flow of knowledge, approvals, permits, licenses to reduce cycle times and costs.
Setting up these supply chains requires a lot of financing, policy and infrastructure support. Schemes such as Production Linked Incentive (PLI) for manufacturing of medical devices and Scheme for Promotion of Manufacturing of Electronic Components and Semiconductors (SPECS) will go a long way in promoting electronic manufacturing in the country.
It is very important to make logistics more efficient - establish deeper connectivity to and from industrial clusters and build interoperable marketplace for end-to-end logistics need. An efficient multi-modal ecosystem of transport needs to be created to lower logistics cost. The government is clearly moving in this direction. An increase in pace would help.
The government needs to continue its thrust on infrastructure building by attracting private investment and making land availability simpler. Labour reforms that make it easier to recalibrate labour contracts as well as a predictable and stable tax regime are cornerstones of an effective industrial policy.
Another area is collaboration. To deal with the unprecedented demands on heath equipment posed by the Covid-19 pandemic, companies responded through unique partnerships. For instance, Ford provided technical and production expertise to manufacture a simplified design of GE Healthcare's existing ventilator to meet the sudden spurt in demand.
A lesson to learn is how the world needs to build more partnerships which leverage agile manufacturing enabled by advanced technology and improved resilience of supply systems for the future.
In conclusion, while the long-term impact of Covid-19 induced changes is yet to be understood, drawing from the lessons so far, it can be seen to be fast accelerating what manufacturers across the world are already focussed on - launching strategic initiatives to build greater resilience and flexibility in supply chains and manufacturing capabilities. It is more than ever evident that new ways of working and manufacturing will have to be rapidly adopted, digitisation of supply chains be accelerated, new partnerships and collaborations forged while delivering value to all stakeholders including to society and environment.