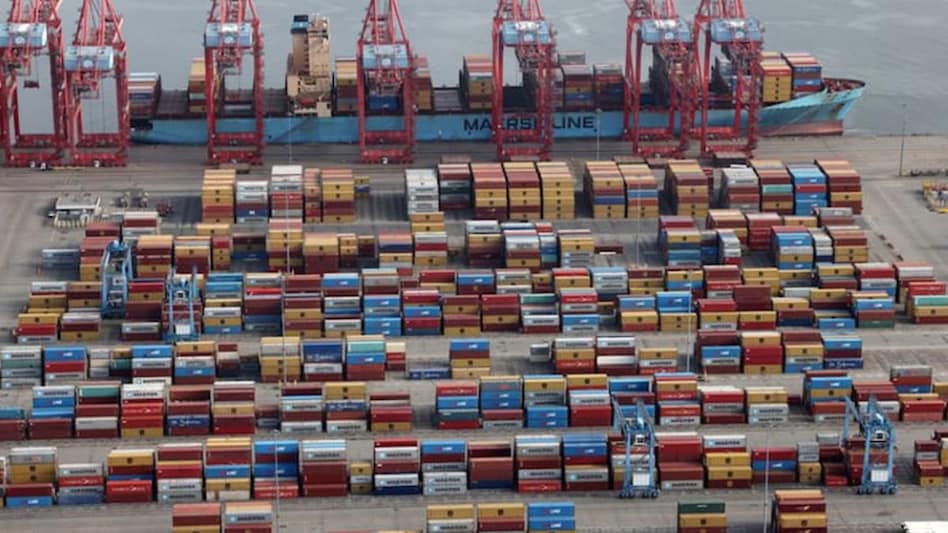
In the past year, much has been written about how global supply chains failed us during the pandemic.
The cause for failure has usually been identified as fragility due to length: as supplier countries scrambled to secure supplies for themselves, global buyers suffered acute shortfalls.
A recent article in the New York Times, (Goodman & Chokshi, June 2021) goes even further: it argues that a key underlying philosophy of supply chain transactions - Just In Time (JIT) - has outlived its usefulness and has not only contributed to the shortages experienced during the worst of Covid but worse still, is to blame for the slow restart many industries are experiencing after covid.
We argue that while Covid taught us valuable lessons, abandoning JIT and related supply chain practices would be a mistake. Instead, it is important to revisit and reengineer our supply chain configurations, based on a deeper understanding of the context.
Also Read: India, Australia must work towards enhancing resilience of supply chains: Piyush Goyal
To make the current thinking concrete, let us take the example of a global shortage unrelated to medical supplies - that of electronic chips.
The shortage in these chips is being felt not only in PCs and smartphones but also in automobile manufacture, which needs the chips for several, computer-controlled systems.
The reason for the chip shortage can be traced to the pandemic: as increasing numbers of employees worked from home, the demand for PC's soared, which resulted in chip shortages not only in the PC industry but other users of chips, such as automotive.
Recent articles blame JIT for the shortage, arguing that JIT and the allied philosophy of 'lean' have given primacy to cost-cutting, which, in turn, puts the screws on inventory holding.
This 'lowest cost' mentality has emptied out inventory pipelines, which are the saviours whenever there is a surge in demand.
We argue that it is not JIT or the lean philosophy that has caused these shortages, it is a flawed interpretation that has distorted fundamentally solid principles and their application.
We also suggest a way out of the dilemma between cost efficiency and lengthy supply chains. To understand the solution, we first need to understand how JIT evolved.
Toyota introduced the concept of the 'Toyota Production System', or TPS, which is a combination of JIT, lean, waste reduction, etc.
Also Read: PLI scheme to benefit domestic auto, parts industries in multiple ways: ICRA
The TPS was, in reality, a graded, evolving response from Toyota to the increasingly competitive markets, and was primarily developed as a tool to align and integrate the 'backend supply chain' with the 'front-end supply chain' by creating linkages, through information generation and sharing.
The knowledge sharing enabled trusted partnerships across the value chain, and with employees. TPS became famous for its quality circles, for instance, where thousands of improvements to the quality of the vehicle were driven by problem-solving from frontline production employees.
Thus, Toyota achieved its legendary reliability and quality, by operating under the four principles (or 4P) framework: philosophy, process, people/ partners and problem-solving.
In this system, JIT and lean were not to be seen as standalone processes to cut costs, but as measures that relied on people/ partners to do their part in continuous problem solving, underpinned by a philosophy that kept the customer's need at its centre.
However, in the US, lean was sold in a way that the US industry would understand easily - overall cost reduction through improved manufacturing practices. Cost reduction was emphasised as it would improve profit. JIT, low inventories, were all options.
Thus, industries in Europe and the US started the practice of the 'Lean Bundle' - a mix of lean management, JIT, waste reduction, process orientation - in the early 1990s.
While TPS regarded the 4P as an integrated whole, the West focused on the harder P's, while de-emphasising the softer Ps of philosophy, people and partners.
Whereas the TPS philosophy sought to keep suppliers and vendors close to the value creator, including through equity holdings and manpower participation (this is typical of Toyota), US and European companies created lengthy, and transaction-oriented 'back-end supply chains' with neither the equity participation nor adequate controls.
The manufacturing industry in the west, led by the automakers, garments, leather goods, and many others went on a cost-cutting binge, by relocating the 'back-end supply chain' to China, India, and other low-cost countries like Vietnam, Thailand, Bangladesh and Philippines.
By 2019, the global manufacturing industry had evolved into a configuration of clusters.
Also Read: Myntra strengthens supply-chain ahead of festive sale with 171 distribution centres
For example, many US and European companies closed down their 'lower value adding' activities in their 'back-end chains' to low-cost centres like China, India and others.
The resulting clustering has created oceans of 'back-end suppliers' and 'value creators', with the whole world being the 'front-end supply chain'.
Such manufacturing chains could withstand Force Majeure conditions of limited impact, in terms of time and magnitude.
But they were not designed to withstand the covid disaster. Even 'holistic clusters', like India and the US, which have large chunks of all the three clusters, quickly ran into critical shortages. Some, such as the scarcity of silicon chips, are yet to be resolved.
As many pundits are proclaiming, Covid may not be the last such pandemic in our lifetimes. And not only biotic but abiotic stresses may create such situations, for which a new term has to be invented because covid was not a force majeure condition.
Covid is something much more than that, both in terms of magnitude and duration of impact. We suggest the term 'Disruption Majeure' for such situations, as they need to be treated differently than the short-lived 'black swan' or force majeure events.
We believe the answer in dealing with such situations is not abandoning processes such as JIT and lean but situating them in a more robust reconfiguration of the manufacturing supply chains.
Manufacturing chains - post covid:
The primary objectives of companies post covid will be 'safe business operations', 'uninterrupted business operations' and 'integrated manufacturing operations'.
These three pillars of post covid business will lead companies to take up multiple actions to redesign the manufacturing value chain in its entirety.
Some of the changes are obvious: Companies are going to get their back-end chains closer to them, geographically. However, in order to still keep cost and supply advantages, some parts of the back-end chain will continue to remain in low-cost but efficient geographies.
Thus, there will be broadly two back-end chains, one, which guarantees supplies during the 'Disruption Majeure' conditions, and the second holds the cost during the normal, day to day business dealings.
In addition to the above, natural progression, we believe that a key success factor for companies will be two, less obvious strategies: First, integrating Industry 4.0 practices (including IoT, Cloud, and AI/ ML) across both supply chains - extended and onshore.
Experts believe that Industry 4.0 is likely to reduce end-to-end delivery cycle times by more than 30%. This will be critical in both supply-chain configurations: offshore and on-shore clusters.
Second, and more counterintuitively, as companies try to ensure 'uninterrupted business operations' they will need to move away from the arms-length transactional, pre-covid world, and instead embrace a fuller interpretation of TPS practices - not as a cost-cutting effort, but as a company managing effort.
This implies full or partial ownership of back-end chains, wasteless, flexible and customer-driven (and lean imputed) value creation chains.
Unfortunately, there is no free lunch here. The downside of this value chain reconfiguration will imply higher costs in the short run - investments in strategic partners, in Industry 4.0 technologies, and changes to governance systems and skill development.
In the long run, these investments will more than pay for themselves, not only in improvement in integrated 4P quality, but also in lower risk in a new 'Disruption Majeure' sensitive world.
(R. Jayaraman is Head of Capstone Projects at Bhavan's SPJIMR and Malay Krishna is Professor and Chairperson, International Relations, Bhavan's SPJIMR.)