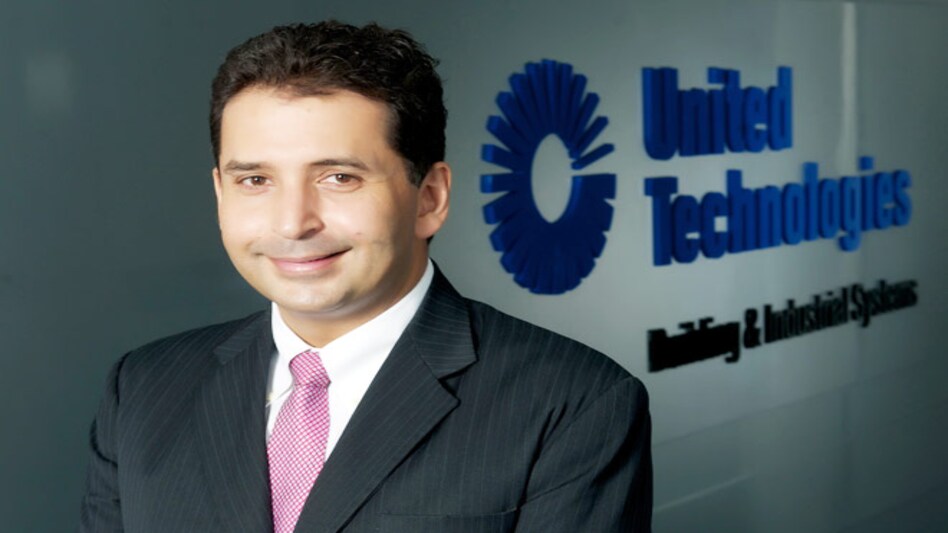
A few days ago when our country's prime minister gave the clarion call of 'Make in India', he didn't just announce a new national programme to foster investment. He also laid out an invite for multinational companies (MNCs) from around the world to truly see the potential that exists in India and capitalize upon it. This vision of our political leadership must be applauded. It should also spur MNCs to come forward to help transform the manufacturing landscape in this country much like the way they have been able to do in the services industry over the last decade or so.
"Make in India" can no longer be seen as "a choice" by MNCs looking to get a bigger pie of the market here. Today, it has become a 'necessity to win'. And there are three reasons for this:
1. Manufacturing locally in India enables companies to make significant savings on import duty and logistics costs, which remain considerably high (up to 25-30% of total landed cost). In UTC's own case, wherever we have localised our products, like chillers and elevators, we have been able to bring the cost down by at least 10-15%, thereby increasing our competitiveness and ability to penetrate new customer segments/ price points.
2. There is also a significant reduction in lead time for deliveries to the customer, especially in the case of complex engineering or high-tech products. Over here, by localising some of our product lines, we have been able to reduce the order to delivery lead time from 12 weeks to as low as four weeks. This allows companies to be far more responsive and flexible to changing customer needs.
3. Local manufacturing also provides an opportunity for MNCs to design and manufacture products that are tailored to Indian operating conditions, which are different compared to other countries - be it how products get transported, how they are installed or under what power conditions they operate. Winning in India requires "designing and manufacturing for India".
While the government has laid out a bold vision to bring more manufacturing to India, companies no doubt will face hurdles in doing so and will need to patiently navigate the path ahead. The core issues impeding the growth of manufacturing today like labour, land, cumbersome taxation systems and poor infrastructure are issues that will take time to solve. The new government has been trying to modify the Factories Act but faces stiff opposition. It is, however, very encouraging to see the recent moves to bring in more transparency around labour inspections and provide more flexibility in the employee provident fund (PF) scheme. The onerous land acquisition bill passed by the earlier government needs to be modified to make it more industry friendly, which is no easy task, and the roll-out of the Goods and Services Tax (GST) will take some time given the fact that every state wants to secure its own financial interests. Most importantly, many of these issues have to be resolved at the state level and we are beginning to see some states surge forward with more progress and reform (for example Gujarat, Rajasthan and Madhya Pradesh). With over $100 billion of investments committed to India by the US, Japan and China during the PM's recent visits, it is up to the states to fight for their respective shares by creating an enabling environment. Those that will do so will receive most of the investment over the next few years. As the environment changes around us and becomes more conducive to manufacturing, there is also a lot that the private industry can do at large (both local and multinational companies), particularly in the areas of attracting talent and developing skills
#1 One issue the manufacturing industry faces is its 'brand image' within today's youth. Unlike the IT or services industry, which are much-aspired for by our young talent, manufacturing does not generate similar interest among young job seekers. According to a survey done by CII and BCG in 2013, less than 15 per cent of Day Zero companies during campus placements were from the manufacturing sector. And 85 per cent of the students indicated that they don't fully understand the true potential of the manufacturing sector. Furthermore, the difference in compensation levels of a manufacturing worker compared that to his/her counterparts in financial or software services is very notable, much higher than it is in countries like the US or China. For entry-level workers in India, this differential is even higher by as much as 30-65%.
Clearly, we all in the manufacturing sector have our work cut out. We need to strive a lot harder to attract and recognise good talent into manufacturing. Countries like Germany and Japan have tried to address this issue by nurturing a"vocational skill" programme where graduates are respected, have better job prospects and compensation. So the pertinent question is: do we as industry value those vocational skills and are we doing enough to build a larger ecosystem to nurture talent that wants to take up the vocational skills? The answer today is, clearly not.
#2 To begin with, as an industry, we can first focus on some very basic 'hygiene' issues like making a common cafeteria, safety, uniforms and other basic amenities available to all the employees irrespective of whether they are permanent or temporary. In fact, it is this differentiation between temporary workforce and permanent employees that lends itself to resentment in the workforce and creates a non-conducive environment.
#3 The other aspect we seriously need to address is creating the right environment for women to work in. After all, diversity is not just a 'good to have' but in a landscape where good talent is harder to come by, the ability to attract more women is a 'strategic advantage'. UTC's Carrier manufacturing facility in Gurgaon, for instance, has piloted a project to create a 'women-only manufacturing line' and all our assessments to date have shown this initiative to be a success. We hope to scale this up and it is critical that other industry players take the issue of increasing its workforce diversity, especially on the shop floor, more seriously.
#4 Finally, for more manufacturing activity to take place in the country, a robust and skilled supply base is required. From UTC's own experience in localising high-engineering products like chillers - a large amount of content still needs to be imported - compressors, tubing due to non-availability of suppliers today. An OEM hence needs to invest in developing supplier capability which can sometimes be a slow and gradual process. Small to Medium Enterprises (SMEs) are going to be critical to the growth of manufacturing in India. This is also an area where industry organisations have a very important role to play. For example, the CII continues to form "clusters" of SMEs within similar trade and provides various development programmes to them. Till date, more than 200 clusters have been formed impacting more than 2,400 companies. This cluster approach helps SMEs to learn through knowledge and best practice sharing, benefiting the industry at large. The MSME (micro, small and medium enterprise) already employs more than 70 million people in the country and multinational companies will have to "step up" and play their part in up-skilling this large workforce.
'Make in India' is going to be a journey. That India has the potential to be a global manufacturing hub cannot be questioned. However, MNCs will need to be patient, invest ahead of the curve and be committed to this opportunity. It's clearly an imperative and no longer an option.
Zubin Irani is the President of UTC Building & Industrial Systems (India Region) and Chairman, CII - Northern Region