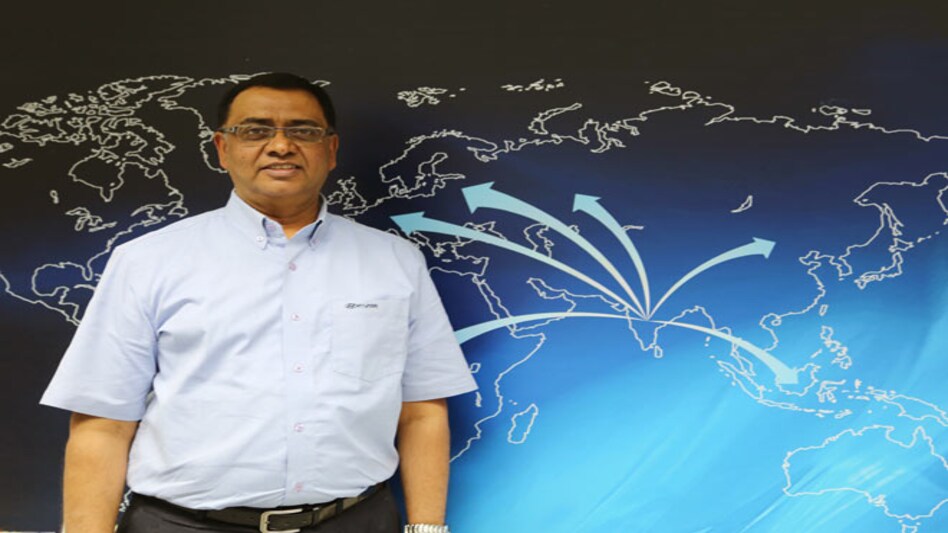
Globally, many carmakers strive for 80 per cent utilisation of capacity. Hyundai's is close to 100 per cent. And that is one of the reasons why it shines bright in the global automotive sky. The utilisation of capacity at Hyundai's India factory, in Sriperumbudur, on the outskirts of Chennai, reflects the heights achieved by its brethren in other parts of the world. In an email interview with Business Today, Stephen Sudhakar J, Vice-President, HR and General Supporting, Hyundai Motor India Ltd (HMIL), explains how this has been achieved and the role played by its workforce. Edited version:
Q. Hyundai Motor India enjoys a very high utilisation of capacity. How has that been achieved?
A. HMIL has a highly-trained manpower and a number of systems working in close co-ordination. We have invested heavily in technology and manpower training to ensure that nothing is left to chance, or open to interpretation. For example, we have inter-linked systems which ensure the required torque is applied on assembly of parts. If not, the conveyor line will stop and everyone in the plant will be alerted.
Similarly, we have an automated system that inspects the engine for 60 critical parts and assemblies. If even one part is missing, the engine will not move to the next station. On the supply side, we choose vendors with proven capability in supplying top-of-the-line products. This is pertinent since 90 per cent of our components are supplier-dependent. Once the products enter our system, we have 500 checkpoints manned by experienced and highly-qualified professionals, who serve as quality gatekeepers.
Q. What is the role of the workforce at your Sriperumbudur factory?
A. People form the core of our existence. We have a well-rounded approach towards our employees on the shop floor. We encourage thinking out of the box. Cutting across rank and file, employees are encouraged and given incentives to experiment. Innovation encourages efficiency, improves design, cuts waste and reduces fatigue. It also helps in increasing employee engagement and development.
We have a programme, "Progress through innovation to deliver excellence", to encourage all workers to look at their operations and give proposals to improve efficiency, safety or reduce costs. These are presented to the senior management each year with the best idea being chosen, implemented and the owner of the idea being rewarded. We also run a campaign called "ACT 302", which stands for "Achieve Challenging Targets, 30 per cent improvements in two years". This is a bottom-up voluntary programme where the employees participate in improving safety, productivity, quality, cost, and ergonomics.
Q. In the recent article that appeared in BT, there was a brief mention about the profile of the technicians with Hyundai India Managing Director Mr. Bo Shin Seo, claiming that the team in HMI is very good with their hands and fingers. Would you like to elaborate further on that to tell us how that has been put to use by the company?
A. Our technicians have a very large part to play in our success. They are mature, talented and have struck a healthy balance between personal and professional goals fulfilling their commitment in their social life as responsible husband, parent, and sibling. Despite the tight work schedules, many of our technicians have gone on to complete their diplomas and degrees after joining the company, which demonstrates their appetite for knowledge through formal education.
Our employees have come up with many productive ideas to cut costs, enhance efficiency, improve quality and ensure safety. In fact our die maintenance technicians and supervisors are considered to be one of the best in the world.
On our part, we have been able to identify this talent and, with a judicious mix of skill and ergonomics, have been able to deploy them to the stations best suited to them. For example, the nimble-fingered are assigned to areas where smaller parts are assembled. Employees of medium physical build are deployed to stations where underbody parts are assembled, minimising the need to bend and yet not missing any part. The idea of deploying employees to stations based on their physique and skills came from the technicians.
The technicians have not limited their suggestions and ideas to their work place alone. They have carried the same principles to their family. Most of them have envisioned a professional career for their children and have enrolled them in good schools. Knowing the importance of all round personality development, they encourage their spouses and children to acquire additional skills and use their time productively. Since many of them live on the outskirts of Chennai, which does not offer too many options, HMIL has organised several co- and extra-curricular programmes where family members are exposed to new skills.
Yoga classes for children and spouses of employees, science clubs, mental maths, cookery classes, English classes and much more have been organised by us from time to time. The recognition they have gained from their peers has not just increased their confidence but also helped them gain respect outside their families. This in turn has had a very positive impact on our employees who come to work in a happy frame of mind. Being stress-free has increased their engagement, fuelling further creativity.
Q. Mr. Seo also said that he has let Indians take leadership roles at the factory. Could you elaborate on how the Indian workforce has led the way?
A. Yes, of course! Indian executives now head divisions like administration, production, sales and marketing and procurement, and are decision makers. Investment in graduate engineer trainee and management trainee programmes has produced a young talent pool with managers in their early thirties capable of leading HMIL over the next two decades. Further investment in our Future Leader Programme) and Global Professional Programme (GPP) has helped groom future leaders to create a talent pipeline that meets the demands of both domestic as well as international operations.
Q. Under the ACT 30 programme, your workers have made a number of suggestions to improve things at the factory. Over Rs 40 crore was saved last year due to these suggestions through 4,000 small projects. Could you give details of how your workers came up with the suggestions, what were some of the more significant suggestions, and how they were implemented?
A. Yes, you are right. We have had considerable saving through ACT 302. Some of the processes have also been replicated in our overseas plants. One of the examples is the Speed Spindle.
The Engine shop uses high-speed spindle in the machining centre to increase productivity in the machining line. A motorised spindle is the rotating part of a machine with an inbuilt motor on which the tool is mounted, which eliminates gear/belt for transferring power. If this spindle gets damaged, the plant will have to wait for six weeks to get it repaired by the manufacturer (mostly an international company). This is an expensive proposition in terms of time and money. To overcome this problem, HMIL developed its own maintenance capability to repair the spindle in-house.
A comprehensive study was done after which special tools were developed for dismantling and assembling the spindle. Simultaneously, a foolproof repair manual was prepared after comprehensive study and training. The efforts resulted in development of localised parts, captive maintenance skills and a special facility for repair. The most important outcome was reducing the downtime to a mere one week and reduction in repair costs.
Q. Hyundai seems to be enjoying peace at the factory after a period of unrest a few years ago. What were the main initiatives that achieved harmonious labour relations?
A. At the outset, let me clarify that labour unrest at our factory, which was witnessed in the past, was an evaluation cum maturation process of granting recognition to the union and not due to any wage-related issue. We rank among one of the best paying companies in the car manufacturing sector and our welfare measures are considered to be one of the best in the industry. In 2011, we recognised an apolitical union which has a proven majority and we always maintain an open channel of communication with it. That guarantees peace and harmony. All issues are discussed and deliberated on in a transparent manner. The union has displayed considerable maturity in ensuring a harmonious working environment and their nominations in several sub-committees, which look into specific operational areas (like transport), is a classic example of how they collaborate with the management for providing effective service and resolution of issues.
In addition, we keep many channels of communication open. Some of them are:
1. My Voice Box
Employees can directly get in touch with the management and expect redressal of their grievances within seven working days. Employees have also given suggestions through this channel for improvisation over the years and an online version of this programme, called "Reach", has also been launched.
2. Lunch Box
The "Best Employee" from every shop has lunch with the top management in an informal setting. This helps both sides understand and assess real issues faced by the employee. It also helps employees appreciate the reasons behind certain decisions taken by the management. This has helped in fostering trust and respect.
Q. What is your wage revision programme and how does it compare with the industry standards?
A. We engage in wage negotiations every three years and, as mentioned earlier, we are one of the best paymasters in the industry.
Copyright©2025 Living Media India Limited. For reprint rights: Syndications Today