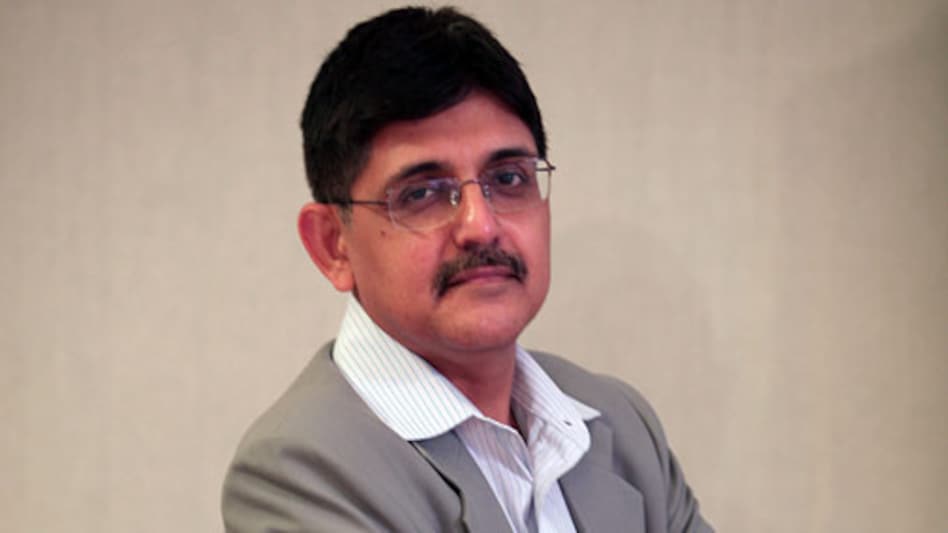
These are tricky times for Indian pharma and they can hardly afford any lapse in their production facilities when the US drug regulator (the US Food and Drug Administration) inspections happen. This is because it will only compound the problems they already have on hand. Already, the USFDA is having to deal with a backlog of around 4,000 generic approval applications (globally, with a good number from India). As is apparent, any issues around good manufacturing practices will only add to the delays for Indian companies.
For instance, Sun Pharmaceuticals, India's leading pharma company is already dealing with issues around its Halol manufacturing plant in Gujarat which faced FDA inspection last year. In fact, in the latest financial results, Dilip Shanghvi, managing director of the company says, "Our performance has been impacted due to various one-time charges, mainly on account of the Ranbaxy merger as well as due to price erosion for some of our products in the US. It also reflects the impact of supply constraints related to the on-going remediation efforts at some of our facilities. We are pledged to being 100 per cent cGMP (current Good Manufacturing Practice) compliant and are fully responsible towards our customers and patients across the world who rely on us for quality products." Dr Reddy's, the NYSE-listed Indian pharma major, is also facing the challenge of slow generic approvals in the US. Some of its critical product approvals in the US have been held up because of the USFDA observations on the company's API (bulk drug) plant in Srikakulam in Andhra Pradesh, which came to light in November last year. The company has subsequently responded to the regulator and hopes to have the concerns sorted out.
Most of the leading Indian pharma companies are already feeling the heat. Nilesh Gupta, Managing Director, Lupin, in a statement following the company's latest financial results, said, "higher price erosion in the US as well as a slowdown in product approvals impacted growth in the quarter."
Add to this, in April this year, the US department of health and human services launched a probe into allegations of generic drug price increases in the US. Also, the pharmacy chains in the US are consolidating and this process will only strengthen their bargaining power and ability to seek discounts from pharma companies. To top it all, there is also a move towards consolidation among big generic pharma companies.
As if this is not enough, Indian pharma companies are also having to deal with currency volatility in the emerging markets, especially in Russia. Two companies that have had to directly deal with this have been Dr Reddy's and Glenmark. "Currency devaluation and subdued business environment persisted to impact our Rest of the World, especially Russian operations," Glenn Saldanha, Chairman & managing director, Glenmark Pharmaceuticals said in a note issued along with the results for the fourth quarter and the financial year. The problem is widespread as is evident from the financial results of some of the leading pharma companies. At a time like this, following good manufacturing practices and having stringent quality controls are conditions that hardly need to be emphasised.
Copyright©2025 Living Media India Limited. For reprint rights: Syndications Today